Amphoteric calcium carbonate filling and preparation method thereof
A calcium carbonate, amphoteric technology, applied in fiber raw material processing, inorganic compound addition, paper and other directions, can solve the problems of incomplete compensation, affecting starch to improve paper dry strength, etc., to improve paper strength, easy control, and improve retention rate Effect
- Summary
- Abstract
- Description
- Claims
- Application Information
AI Technical Summary
Problems solved by technology
Method used
Examples
Embodiment 1
[0030] Raw material formula: collagen 0.16g, calcium chloride 4.8g, sodium carbonate 5.3g, water 250ml.
[0031] Mix 4.8g of calcium chloride and 5.3g of sodium carbonate evenly, dissolve 0.16g of collagen in 250ml of water, and slowly add to the mixture of calcium chloride and sodium carbonate. The reaction was left to stand at 4°C for 7 days, filtered with suction, washed with water, and freeze-dried.
Embodiment 2
[0033] Raw material formula: gelatin 30.0g, calcium chloride 85.0g, sodium carbonate 53.0g, water 1000ml.
[0034] Dissolve 85.0g of calcium chloride and 53.0g of sodium carbonate in 200ml of water, and then mix evenly. Dissolve 30.0g of gelatin in 800ml of water and slowly add to the mixture of calcium chloride and sodium carbonate. Stand at room temperature and react for 1 day, centrifuge, wash with water, and dry in vacuum.
Embodiment 3
[0036] Raw material formula: gelatin 15.0g, calcium chloride 28.0g, sodium carbonate 24.0g, water 600ml.
[0037] Mix 28.0 g of calcium chloride and 24.0 g of sodium carbonate, dissolve 15.0 g of gelatin in 600 ml of water, and slowly add to the mixture of calcium chloride and sodium carbonate while stirring. Stir at room temperature for 2 hours, let stand for 30 minutes, filter, wash with water, and dry at room temperature.
PUM
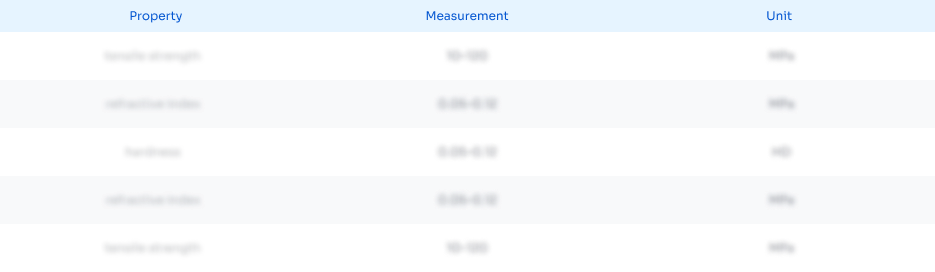
Abstract
Description
Claims
Application Information

- R&D
- Intellectual Property
- Life Sciences
- Materials
- Tech Scout
- Unparalleled Data Quality
- Higher Quality Content
- 60% Fewer Hallucinations
Browse by: Latest US Patents, China's latest patents, Technical Efficacy Thesaurus, Application Domain, Technology Topic, Popular Technical Reports.
© 2025 PatSnap. All rights reserved.Legal|Privacy policy|Modern Slavery Act Transparency Statement|Sitemap|About US| Contact US: help@patsnap.com