Method of producing fir chemical pulp
A technology for chemical pulp and production methods, which is applied in papermaking, textile and papermaking, and the manufacture of thin wood chips, etc., can solve the problems of reduced pulp production capacity, long cooking cycle, and high alkali consumption, and achieves improved utilization efficiency, short cooking cycle, Low alkalinity effect
- Summary
- Abstract
- Description
- Claims
- Application Information
AI Technical Summary
Problems solved by technology
Method used
Image
Examples
Embodiment 2
[0025] The production method of embodiment 2 is as follows:
[0026] (1) Material preparation: choose peeled fir, send it to the chipper to cut into wood chips, and the wood chips are screened by a swing screen to select qualified wood chips with a length of 12-45mm, a width of 10-50mm, and a thickness of 2-9mm, and send them to the silo or feeder. On-site storage, the pass rate of tested wood chips is 73%;
[0027] (2) Pot loading: After the cooking pot 5 has been sprayed, open the pot cover and the gate 3 of the wood chip bin 1, and the wood chips after the process (1) will be packed into the cooking pot 5 through the wood chip bin 1. In the process, add 23.5% (NaOH meter, weight ratio to absolute dry wood chips), degree of sulfidation 20%, kraft method cooking liquid with liquid ratio 1: 3.2, close feed bin gate 3 after installing, and cover the pot cover;
[0028] (3) Cooking: The material in the pot after the process (2) is directly heated from the steam inlet pipe and ...
Embodiment 3
[0031] The production procedure of embodiment 3 is as follows:
[0032] (1) Material preparation: choose peeled fir, send it to the chipper and cut it into wood chips, and the wood chips are screened by a swing screen to select qualified wood chips with a length of 12-45mm, a width of 10-50mm, and a thickness of 2-9mm, according to the dry weight ratio Mix less than 30% Chinese fir chips and more than 70% masson pine chips with the same specifications, and send them to the silo or stockyard for storage. The passing rate of the tested wood chips is 82%;
[0033] (2) Pot loading: After the cooking pot 5 has been sprayed, open the pot cover and the gate 3 of the wood chip bin 1, and the wood chips after the process (1) will be packed into the cooking pot 5 through the wood chip bin 1. In the process, add 24% (NaOH meter, weight ratio to absolute dry wood chips), degree of sulfidation 22%, and kraft method cooking liquid with a liquid ratio of 1: 2.7, close the feed bin gate 3 aft...
PUM
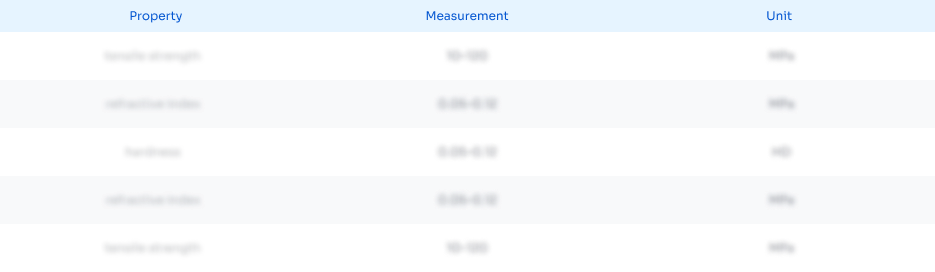
Abstract
Description
Claims
Application Information

- R&D
- Intellectual Property
- Life Sciences
- Materials
- Tech Scout
- Unparalleled Data Quality
- Higher Quality Content
- 60% Fewer Hallucinations
Browse by: Latest US Patents, China's latest patents, Technical Efficacy Thesaurus, Application Domain, Technology Topic, Popular Technical Reports.
© 2025 PatSnap. All rights reserved.Legal|Privacy policy|Modern Slavery Act Transparency Statement|Sitemap|About US| Contact US: help@patsnap.com