Production method for graving gravure on-machine plate
A production method and plate base technology, which are applied in the direction of photomechanical processing of originals for photomechanical processing, photographic process of pattern surface, optics, etc., can solve the problems of high cost of plate making, low production efficiency, complicated steps, etc., and achieve plate making The effect of shortening the cycle, accurate specifications and sizes, and reducing the cost of plate making
- Summary
- Abstract
- Description
- Claims
- Application Information
AI Technical Summary
Problems solved by technology
Method used
Examples
Embodiment 1
[0011] Plate making according to the method for making a machine printing plate for engraving gravure printing of the present invention:
[0012] First of all, the surface treatment of the brass plate purchased in the market is used as the plate base material for the printing plate on the machine.
[0013] Then, use a computer to design the graphics and texts to be printed, prepare a film, coat the photosensitive material on the plate base, cover the film on the metal plate base after drying, and perform exposure. The exposed photosensitive adhesive forms a photopolymerization reaction. , has the ability to resist water and corrosion, wash off the unexposed photosensitive adhesive with water to expose the metal surface;
[0014] After the exposure is completed, the plate substrate is immersed in an etching solution prepared with ferric chloride for etching. The part not covered by the photosensitive adhesive, that is, the part that needs to be recessed, will be etched away. Th...
Embodiment 2
[0017] Plate making according to the method for making a machine printing plate for engraving gravure printing of the present invention:
[0018] Firstly, process and clean the steel plate purchased in the market to make a steel plate base;
[0019] Then make the photosensitive film to be printed and cover it on the stencil base, and perform exposure treatment. After exposure, use sulfuric acid, nitric acid or hydrochloric acid and other corrosive solutions to corrode the plate base, and clean away the parts that need to be recessed;
[0020] After the first etching, the photosensitive film can be covered again on the corroded graphic surface to protect it, and then the graphic part that needs to be deepened and widened can be etched a second time;
[0021] Finally, the surface layer of the corroded plate base is chrome-plated, that is, the production of the completed printing plate.
[0022] The prepared printing plate can be directly printed on the machine, which greatly sh...
Embodiment 3
[0024] Electroplate a copper layer of about 0.15 mm on the surface of the nickel plate base, and process it on a grinding machine to the standard thickness of the gravure plate on the upper machine before use.
[0025] Apply photosensitive glue on the copper layer of the prefabricated plate, and carry out printing treatment. After aging, the non-patterned part of the photosensitive glue will form a water-resistant and corrosion-resistant protective layer. The unphotosensitive patterned part will be washed with water, and the photosensitive glue will fall off and be exposed. out of the copper layer. Then put the plate in the corrosion machine, spray impact on the plate surface with ferric chloride solvent, the copper layer of the exposed part is dissolved, and a depression is formed. After reaching the predetermined depth, rinse, degumming, and chrome plating on the surface, it can be finished. As a machine engraving gravure plate.
[0026] The preparation method of the presen...
PUM
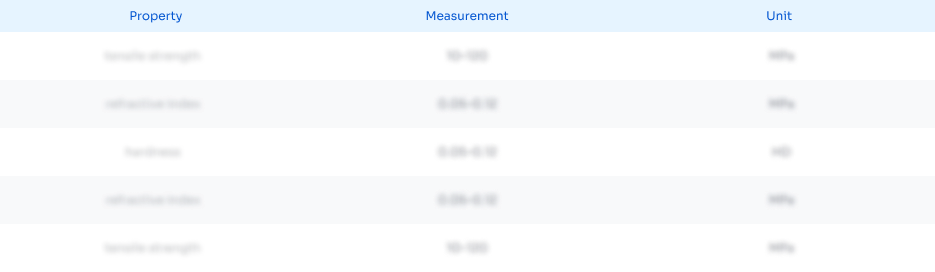
Abstract
Description
Claims
Application Information

- R&D Engineer
- R&D Manager
- IP Professional
- Industry Leading Data Capabilities
- Powerful AI technology
- Patent DNA Extraction
Browse by: Latest US Patents, China's latest patents, Technical Efficacy Thesaurus, Application Domain, Technology Topic, Popular Technical Reports.
© 2024 PatSnap. All rights reserved.Legal|Privacy policy|Modern Slavery Act Transparency Statement|Sitemap|About US| Contact US: help@patsnap.com