Method for preparing stannic oxide hollow sphere
A technology of tin dioxide and nano-tin dioxide, applied in the direction of tin oxide, etc., can solve the problems of large-scale industrial production limitations, complex process steps, environmental pollution, etc., and achieve the effect of low cost, simple production process and low price
- Summary
- Abstract
- Description
- Claims
- Application Information
AI Technical Summary
Problems solved by technology
Method used
Image
Examples
Embodiment 1
[0022] (1) Pretreatment: In the reaction tank, 5g SnCl 4 ·5H 2 O was dissolved in 80 g of distilled water, and the pH value of the system was adjusted to 10 with NaOH, which was recorded as solution A.
[0023] (2) Material impregnation: Then 10 g of sycamore sawdust was added to solution A, and after impregnation at room temperature for 7 days, the impregnation was vacuum filtered and dried at room temperature to obtain impregnated sawdust powder.
[0024] (3) Heat treatment: Put the impregnated sawdust into the muffle furnace, keep the temperature of the furnace at 400°C for 20 hours, then cool down and discharge the material to produce tin dioxide hollow spheres.
[0025] Fig. 1 is the X-ray crystal diffraction spectrum of the tin dioxide hollow sphere material prepared according to embodiment 1, and the diffraction peak position shows that it is pure rutile tin dioxide. Fig. 2, Fig. 3 are respectively the low magnification TEM photo and the high magnification TEM photo o...
Embodiment 2
[0027] (1) Pretreatment: In the reaction tank, 1.5g SnCl 4 ·5H 2 O was dissolved in 148.5 g of distilled water, and the pH value of the system was adjusted to 10 with NaOH, which was recorded as solution A.
[0028] (2) Material impregnation: Then add 1.5 g of French sycamore sawdust to solution A, and after impregnating at room temperature for 7 days, vacuum filter the impregnated material, and dry at room temperature to obtain impregnated sawdust powder.
[0029] (3) Heat treatment: Put the impregnated sawdust into the muffle furnace, keep the temperature of the furnace at 400°C for 20 hours, then cool down and discharge the material to produce tin dioxide hollow spheres.
Embodiment 3
[0031] (1) Pretreatment: In the reaction tank, 25g SnCl 4 ·5H 2 O was dissolved in 100 g of distilled water, and the pH value of the system was adjusted to 12 with NaOH, which was recorded as solution A.
[0032] (2) Material impregnation: Then, 7.5 g of Paulownia sawdust was added to solution A, and after impregnation at room temperature for 5 days, the impregnation was vacuum filtered and dried at room temperature to obtain impregnated sawdust powder.
[0033] (3) Heat treatment: put the impregnated sawdust into a muffle furnace, keep the temperature of the furnace at 500°C for 10 hours, cool down and discharge the material to produce tin dioxide hollow spheres.
PUM
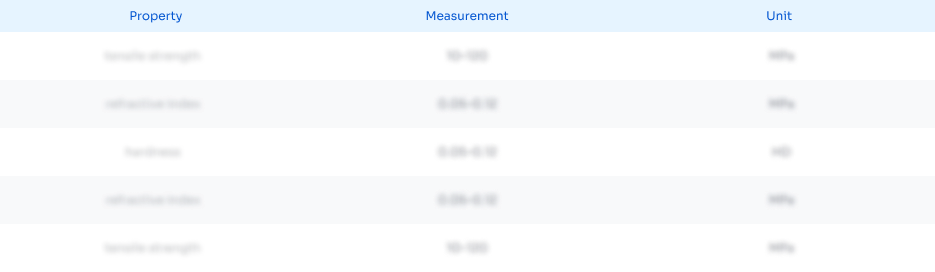
Abstract
Description
Claims
Application Information

- Generate Ideas
- Intellectual Property
- Life Sciences
- Materials
- Tech Scout
- Unparalleled Data Quality
- Higher Quality Content
- 60% Fewer Hallucinations
Browse by: Latest US Patents, China's latest patents, Technical Efficacy Thesaurus, Application Domain, Technology Topic, Popular Technical Reports.
© 2025 PatSnap. All rights reserved.Legal|Privacy policy|Modern Slavery Act Transparency Statement|Sitemap|About US| Contact US: help@patsnap.com