Aluminum, aluminum alloy and composite material ultrasonic vibration liquid phase welding equipment therefor
A composite material, ultrasonic vibration technology, applied in welding equipment, non-electric welding equipment, metal processing equipment and other directions, to achieve ideal engineering significance, flexible welding operation, flexible introduction position
- Summary
- Abstract
- Description
- Claims
- Application Information
AI Technical Summary
Problems solved by technology
Method used
Image
Examples
Embodiment Construction
[0020] The present invention is described in more detail below in conjunction with accompanying drawing example:
[0021] Combined with Figure 1, the ultrasonic vibration liquid phase welding equipment for aluminum, aluminum alloys and their composite materials includes a control box 1, a support 3 is installed at the bottom of the control box, an ultrasonic generator is installed in the control box, and the panel of the control box is set There are control buttons and terminal posts 2. The upper surface of the control box is a clamping work platform 4. A bracket is set above the control box. The temperature display panel 6 and the ultrasonic welding head are respectively installed on the bracket. One end of the thermocouple is connected with the workpiece to be tested, and the other is One end is connected with the temperature control module 7 and the temperature display panel through the terminal post on the control panel, and the temperature is displayed from the temperature...
PUM
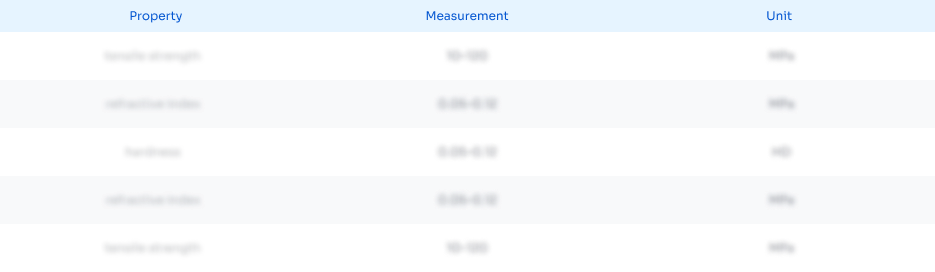
Abstract
Description
Claims
Application Information

- R&D
- Intellectual Property
- Life Sciences
- Materials
- Tech Scout
- Unparalleled Data Quality
- Higher Quality Content
- 60% Fewer Hallucinations
Browse by: Latest US Patents, China's latest patents, Technical Efficacy Thesaurus, Application Domain, Technology Topic, Popular Technical Reports.
© 2025 PatSnap. All rights reserved.Legal|Privacy policy|Modern Slavery Act Transparency Statement|Sitemap|About US| Contact US: help@patsnap.com