Flame resisting wave-absorbing material and method for making same
A wave-absorbing material and flame-retardant technology, which is applied to the parts, shielding, and instruments of instruments, can solve the problems affecting the surface appearance quality of wave-absorbing materials, poor surface cleanliness, and poor anti-pollution ability of wave-absorbing materials, and achieve Save firefighting capital investment, solve fire safety hazards, and enhance adhesion
- Summary
- Abstract
- Description
- Claims
- Application Information
AI Technical Summary
Problems solved by technology
Method used
Image
Examples
Embodiment 1
[0034] Use impregnated non-woven fabric as the matrix; put 40 parts of aluminum-magnesium composite powder, 23 parts of organic adhesive (such as polyvinyl alcohol glue), 7.5 parts of silica sol, 0.1 part of defoamer and 29 parts of water into the disperser respectively Stir and disperse evenly to make a flame-retardant coating; grind the prepared flame-retardant coating with a three-roller grinder to make the coating uniform and fine; add the flame-retardant coating to the tank of the special flame-retardant mechanical brushing equipment, The non-woven fabric is immersed in the flame-retardant coating through the pressure roller, and the 15m long drying tunnel is opened, and the other end of the drying tunnel starts to wind the non-woven fabric, and the flame-retardant coating is evenly coated on the non-woven fabric, and dried; the carbon black 3 38 parts, 38 parts of organic adhesive (such as polyvinyl alcohol glue), 0.1 part of defoamer, 1 part of dispersant, and 57 parts o...
Embodiment 2
[0041] It is basically the same as Example 1, except that the flame retardant coating is prepared as follows: 35 parts of aluminum hydroxide, 20 parts of organic adhesive, 6 parts of silica sol, 0.1 part of defoamer, and 25 parts of water. The conductive coating is prepared as follows: 2.5 parts of acetylene carbon black, 35 parts of organic adhesive, 0.1 part of defoamer, 0.8 part of dispersant, and 50 parts of water.
Embodiment 3
[0043] It is basically the same as Example 1, except that the flame retardant coating is prepared as follows: 45 parts of magnesium hydroxide, 30 parts of organic adhesive, 10 parts of silica sol, 0.3 parts of defoamer, and 35 parts of water. The conductive coating was prepared as follows: 3.4 parts of acetylene carbon black, 42 parts of organic adhesive, 0.3 parts of defoamer, 1.2 parts of dispersant, and 60 parts of water.
PUM
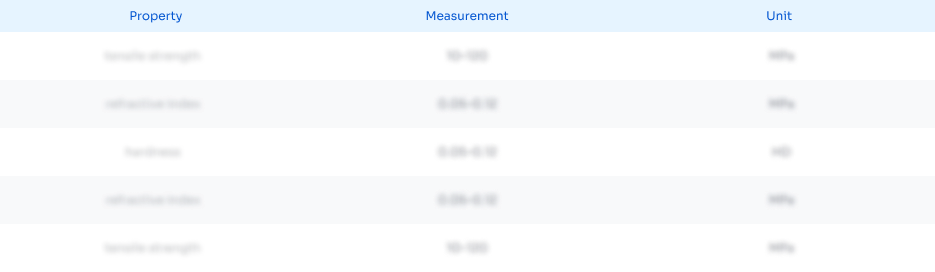
Abstract
Description
Claims
Application Information

- Generate Ideas
- Intellectual Property
- Life Sciences
- Materials
- Tech Scout
- Unparalleled Data Quality
- Higher Quality Content
- 60% Fewer Hallucinations
Browse by: Latest US Patents, China's latest patents, Technical Efficacy Thesaurus, Application Domain, Technology Topic, Popular Technical Reports.
© 2025 PatSnap. All rights reserved.Legal|Privacy policy|Modern Slavery Act Transparency Statement|Sitemap|About US| Contact US: help@patsnap.com