Process for preparing composite photochromic optical resin lens
An optical resin lens and photochromic technology, applied in optics, optical components, glasses/goggles, etc., can solve the problems of uneven color changing layer, insensitive response, etc., achieve high light transmittance, eliminate dispersion, and polymerize The effect of uniform and stable material structure
- Summary
- Abstract
- Description
- Claims
- Application Information
AI Technical Summary
Problems solved by technology
Method used
Image
Examples
Embodiment 1
[0030] Prepare 350 base-layer lenses, after surface treatment by alkali etching, cleaning, drying, ion beam, and gluing, inspect and close the mold, and the thickness of the mold is 1.0 mm. Take 1.9Kg of chemical monomer benzyl methacrylate and 2,4-bis[4-(formylpolyethoxy)phenyl]propane in a ratio of 6:4, and add 98.77g of 2 in turn while stirring, 4-diphenyl-4-methyl-1-pentene, then add 30mg of graying dye, after stirring evenly, add 0.6g of tert-butyl peroxyneodecanoate and 0.6g of tert-butyl peroxy-2-ethyl For tert-butyl hexanoate, after stirring for 3 hours, vacuumize at -0.095Mpa for 15 minutes. Filter casting under pressure 0.05MPa, and cure with the following curing curve:
[0031] Start temperature at 35°C for 8 hours, rise to 40°C after 14 hours, rise to 50°C after 8 hours, rise to 85°C after 10 hours, then keep warm for 4 hours, drop to 50°C after 2 hours, and then furnace after 46 hours When the temperature is 50°C, take out the tape and put it in normal temperatu...
Embodiment 2
[0033] Prepare 200 base-layer lenses, after surface treatment, check the mold closing, the thickness of the mold closing is 1.2mm. Take 1.8Kg chemical monomers benzyl methacrylate and 2,4-bis[4-(formylpolyethoxy)phenyl]propane in a ratio of 6:4, and add 100g of 2,4 -diphenyl-4-methyl-1-pentene, then add 50mg of graying dye, after stirring well, add 0.4g of tert-butyl peroxyneodecanoate and 0.4g of 2-ethylhexyl peroxide Acetate tert-butyl ester, after stirring for 4 hours, vacuumize for 15 minutes under the vacuum degree of -0.090MPa. Filter casting under pressure 0.05MPa, and cure with the following curing curve:
[0034] Start temperature at 35°C for 10 hours, rise to 40°C after 12 hours, rise to 50°C after 10 hours, rise to 85°C after 6 hours, then keep warm for 4 hours, drop to 50°C after 2 hours, and then furnace after 44 hours When the temperature is 50°C, take out the adhesive tape and put it in normal temperature water, remove the mold, take out the lens and then clea...
PUM
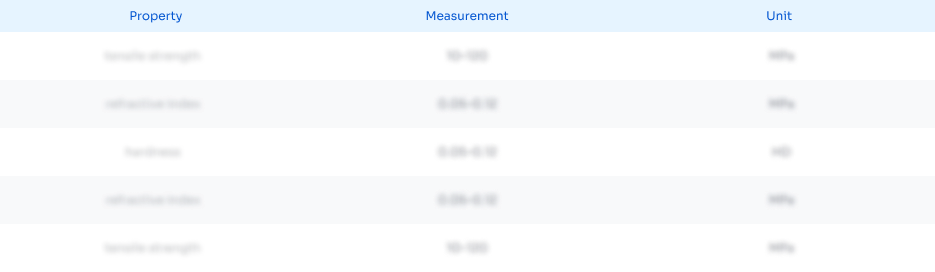
Abstract
Description
Claims
Application Information

- Generate Ideas
- Intellectual Property
- Life Sciences
- Materials
- Tech Scout
- Unparalleled Data Quality
- Higher Quality Content
- 60% Fewer Hallucinations
Browse by: Latest US Patents, China's latest patents, Technical Efficacy Thesaurus, Application Domain, Technology Topic, Popular Technical Reports.
© 2025 PatSnap. All rights reserved.Legal|Privacy policy|Modern Slavery Act Transparency Statement|Sitemap|About US| Contact US: help@patsnap.com