Preparation method of Cu.TiB nano-diffusion alloy
A cu-tib2 alloy technology, applied in the field of Cu-TiB2 alloy and its preparation, can solve the problems of complex alloy process and difficult process control, and achieve the effects of low preparation cost, easy control and simple production equipment
- Summary
- Abstract
- Description
- Claims
- Application Information
AI Technical Summary
Problems solved by technology
Method used
Image
Examples
Embodiment 1
[0013] Example 1: The alloy composition is TiB 2 -0.25wt%, the rest is copper and unavoidable impurities. The raw materials for preparing the alloy are Cu-0.34wt% Ti and Cu-0.17wt% B. figure 2 After melting in the two crucibles in the device shown, after overheating to 1350℃, use 2×10 5 Pa of high pressure and high purity N 2 The gas presses the alloy melt into the reaction chamber from the two pipes, so that the two melts react in situ when they collide with each other and mix to form TiB 2 A homogeneous mixture of nanoparticles and pure copper melt. The mixture is quickly condensed by spray deposition. The conditions of spray deposition are: Pressure: 3×10 5 ~6×10 5 Pa, atomizing gas: N 2 Gas to make Cu-TiB 2 The alloy billet is then hot rolled and cold rolled into a thin plate with a thickness of 0.30 mm. The main properties are shown in Table 1. For the sake of comparison, the corresponding properties of TU1 pure copper are also listed in Table 1 (both alloys were annealed wi...
Embodiment 2
[0016] Example 2: The alloy composition is TiB 2 -0.5wt%, the rest is copper and unavoidable impurities. The raw materials for preparing the alloy are Cu-0.68wt% Ti and Cu-0.34wt% B. figure 2 After the two crucibles in the device shown are melted and overheated to 1350℃, use 2×10 5 The high-pressure and high-purity Ar gas of Pa presses the alloy melt into the reaction chamber from the two pipes respectively, so that the two melts react in situ when they collide and mix to form TiB. 2 A homogeneous mixture of nanoparticles and pure copper melt. The mixture is quickly condensed by spray deposition. The conditions of spray deposition are: Pressure: 3×10 5 ~6×10 5 Pa, atomizing gas: Ar gas, made of Cu-TiB 2 The alloy billet is hot-extruded and cold-drawn into a Φ12 bar. Its main performance is shown in Table 2. For the convenience of comparison, Cu-0.35wt% Al is also listed in Table 2 2 O 3 Corresponding performance of the dispersion strengthened copper alloy (both alloys are annealed...
PUM
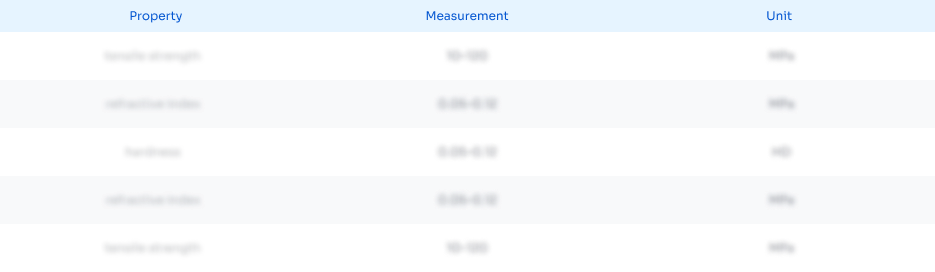
Abstract
Description
Claims
Application Information

- R&D
- Intellectual Property
- Life Sciences
- Materials
- Tech Scout
- Unparalleled Data Quality
- Higher Quality Content
- 60% Fewer Hallucinations
Browse by: Latest US Patents, China's latest patents, Technical Efficacy Thesaurus, Application Domain, Technology Topic, Popular Technical Reports.
© 2025 PatSnap. All rights reserved.Legal|Privacy policy|Modern Slavery Act Transparency Statement|Sitemap|About US| Contact US: help@patsnap.com