Light-emitting device of gallium nitride compound semiconductor
- Summary
- Abstract
- Description
- Claims
- Application Information
AI Technical Summary
Benefits of technology
Problems solved by technology
Method used
Image
Examples
example 1
The present invention will be described in more detail with reference to a first disclosed embodiment. FIG. 1 shows a vertical section of a light-emitting diode 10 pertaining to the present invention. It has a sapphire substrate 1, on which there are successively formed a buffer layer 2 of AlN (500 .ANG. thick), a high-carrier density n.sup.+ -layer 3 of GaN (2.2 .mu.m thick), a low-carrier density n-layer 4 of GaN (1.5 .mu.m thick), an .[.i-layer.]. .Iadd.a p-type impurity doped layer .Iaddend.5 of GaN (0.1 .mu.m thick), an electrode 7 of aluminum, and an electrode 8 of aluminum (in contact with the high-carrier density n.sup.+ -layer 3).
This light-emitting diode 10 is produced by the steps which are explained below with reference to FIGS. 2(A) to 4(C).
The entire process was carried out using NH.sub.3, H.sub.2 (carrier gas), trimethyl gallium Ga(CH.sub.3).sub.3 (TMG for short), trimethyl aluminum Al(CH.sub.3).sub.3 (TMA for short), silane SiH.sub.4 and diethyl zinc (DEZ for short)....
example 2
A light-emitting diode was prepared in the same manner as in Example 1. As shown in FIG. 6, it is composed of a sapphire substrate 1, a buffer layer 2 of AlN, a high-carrier density n.sup.+ -layer 3 of GaN, a low-carrier density n-layer 4 (1.1 .mu.m thick) having a carrier density of 1.times.10.sup.15 / cm.sup.3, a low-impurity density .[.i.sub.L -layer.]. .Iadd.L-layer .Iaddend.51 (1.1 .mu.m thick) having a Zn density of 2.times.10.sup.18 / cm.sup.3, and a high-impurity density .[.i.sub.H -layer.]. .Iadd.H-layer .Iaddend.52 (0.2 .mu.m thick) having a Zn density of 1.times.10.sup.20 / cm.sup.3. It should be noted that the .[.i-layer.]. .Iadd.p-impurity doped layer .Iaddend.is of dual structure with 51 and 52.
A hole 60 was formed which penetrates the high-impurity density .[.i.sub.H layer.]. .Iadd.H-layer .Iaddend.52, the low-impurity density .[.i.sub.L layer.]. .Iadd.L-layer .Iaddend.51, and the low-carrier density n-layer 4, reaching the high-carrier density n.sup.+ -layer 3. In this ...
example 3
The light-emitting diode in this example differs from that in the previous example in that the first Ni layer 71 (81) and second Ni layer 72 (82) are replaced by a Ni layer 710 (810) of single-layer structure, which is 300 .ANG. thick, as shown in FIG. 7. This difference in structure has nothing to do with its performance. The Ni layer 710 (810) should preferably have a thickness in the range of 50 .ANG. to 3000 .ANG.. With a thickness lower than specified, it will be subject to attack by solder when a solder bump is formed. With a thickness greater than specified, it causes the light source to be localized near the electrode rather than the center and it is liable to peeling at the time of soldering in a solder bath.
PUM
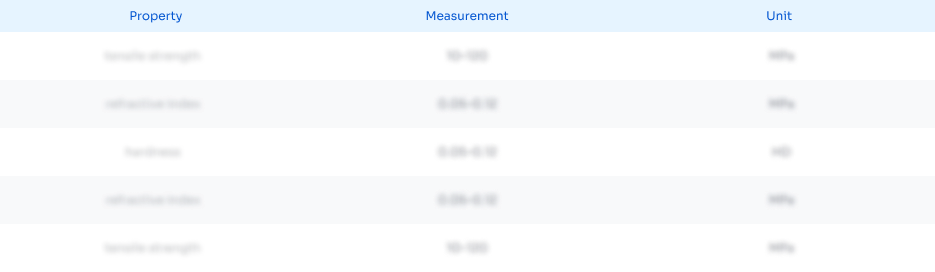
Abstract
Description
Claims
Application Information

- R&D
- Intellectual Property
- Life Sciences
- Materials
- Tech Scout
- Unparalleled Data Quality
- Higher Quality Content
- 60% Fewer Hallucinations
Browse by: Latest US Patents, China's latest patents, Technical Efficacy Thesaurus, Application Domain, Technology Topic, Popular Technical Reports.
© 2025 PatSnap. All rights reserved.Legal|Privacy policy|Modern Slavery Act Transparency Statement|Sitemap|About US| Contact US: help@patsnap.com