Tapping atomic force microscope with phase or frequency detection
- Summary
- Abstract
- Description
- Claims
- Application Information
AI Technical Summary
Benefits of technology
Problems solved by technology
Method used
Image
Examples
Embodiment Construction
The present invention utilizes the inventors' discovery that if the probe is oscillated at or near one of the resonant frequencies of the lever, that in fact the probe tip has much less of a tendency to stick to the surface because a resonant system tends to remain in stable oscillation even if some damping exists. Thus the preferred embodiment of the present invention utilizes a resonant oscillation of the cantilever at sufficient oscillation amplitude to achieve the advantages described above without the probe becoming stuck to the surface. This preferred embodiment also provides many of the benefits of the non-contact AFM as described above.
Existing development of AFM's using oscillation of the probes has been directed at avoiding surface contact, as described above, and as such is limited in practicality despite the potential advantages of the technique. For applications where the non-contact mode is desired, the inventors have found that the amplitude-distance curve of FIG. 6 c...
PUM
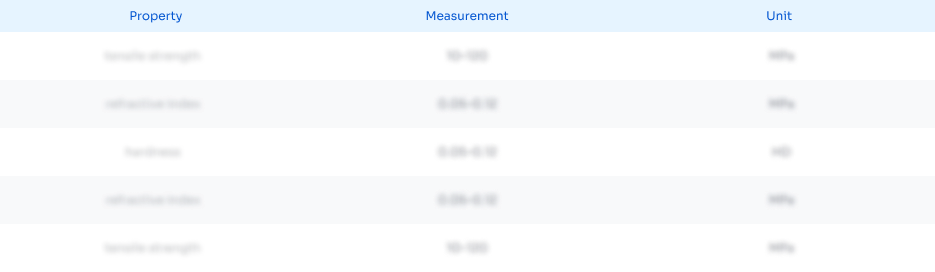
Abstract
Description
Claims
Application Information

- R&D
- Intellectual Property
- Life Sciences
- Materials
- Tech Scout
- Unparalleled Data Quality
- Higher Quality Content
- 60% Fewer Hallucinations
Browse by: Latest US Patents, China's latest patents, Technical Efficacy Thesaurus, Application Domain, Technology Topic, Popular Technical Reports.
© 2025 PatSnap. All rights reserved.Legal|Privacy policy|Modern Slavery Act Transparency Statement|Sitemap|About US| Contact US: help@patsnap.com