Method of forming wirings for tile-shaped elements, structures of wirings for tile-shaped elements, and electronic equipment
a technology of wiring and tile, applied in the direction of conductive pattern formation, thermoelectric devices, printed circuit non-printed electric components association, etc., can solve the problems of substantial time required for wiring work, substantially large manufacturing cost, so as to reduce the waste of liquid material, excellently formed, and high reliability
- Summary
- Abstract
- Description
- Claims
- Application Information
AI Technical Summary
Benefits of technology
Problems solved by technology
Method used
Image
Examples
first exemplary embodiment
[0040]A wiring forming method for a tile-shaped element and a wiring structure for a tile-shaped element in accordance with a first exemplary embodiment of the invention are described below. As an example of a tile-shaped element in accordance with the present exemplary embodiment, a micro tile-shaped element in a minute tile configuration is described. However, the invention is not limited to this, and can be applied to a tile-shaped element that is not minute. First, a wiring forming method for a tile-shaped element and a wiring structure for a tile-shaped element in accordance with the first exemplary embodiment of the invention are described with reference to FIGS. 1A–B and FIGS. 2A–B.
[0041]FIGS. 1A–B are schematics in which a micro tile-shaped element is bonded to a final substrate. A micro tile-shaped element 1 is equipped with a tile section 11 in a tile configuration and an electrode 21 provided on an upper surface of the tile section 11. The tile section 11 may have a funct...
examples of application
Method
[0050]Next, examples of the method of applying the liquid material 53 to the wiring region 61 are described. For example, a method in which the liquid material 53 is once applied to the entire surface of the final substrate 50 including the surface of the minute tile element 1, and then, the liquid material 53 applied on areas other than the wiring region 61 is removed, to thereby coat the liquid material only on the wiring region 61, can be used. However, according to this method, the amount of the liquid material 53 that becomes wasted is large. Thus, it is desirable to use a method in which the liquid material 53 is initially, selectively applied only to the wiring region 61.
[0051]A droplet discharge method to jet the liquid material 53 as droplets from an ink jet nozzle, that may be used with, for example, an ink-jet printer, or the like, can be used as the method to selectively apply the liquid material 53. Moreover, the liquid material 53 may be discharged as droplets by...
second exemplary embodiment
[0055]Next, a wiring forming method for a tile-shaped element and a wiring structure for a tile-shaped element in accordance with a second exemplary embodiment of the invention are described below with reference to FIGS. 3A–B through FIGS. 5A–B. First, a micro tile-shaped element 1a to which the wiring forming method of the present exemplary embodiment is applied is described. FIGS. 3A–B show an example of a micro tile-shaped element in accordance with the second exemplary embodiment. The micro tile-shaped element 1a is a minute semiconductor element in a tile configuration. The micro tile-shaped element 1a is formed from a plate-like member having a thickness of 20 μm or less, and a size in width and length of several ten μm to several hundred μm. In a method for manufacturing the micro tile-shaped element 1a, a sacrificial layer is formed on a semiconductor substrate (first substrate), and a functional layer (electronic functional section) that defines the micro tile-shaped elemen...
PUM
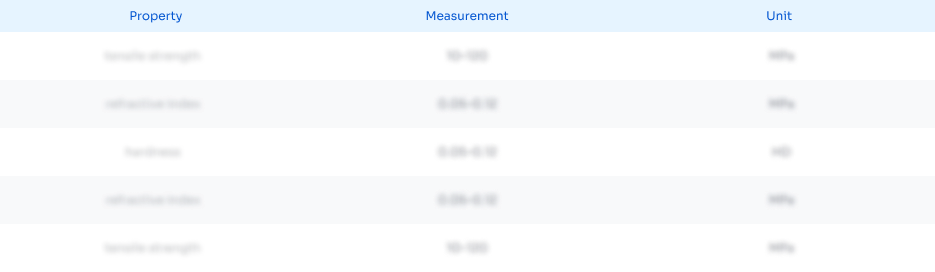
Abstract
Description
Claims
Application Information

- R&D
- Intellectual Property
- Life Sciences
- Materials
- Tech Scout
- Unparalleled Data Quality
- Higher Quality Content
- 60% Fewer Hallucinations
Browse by: Latest US Patents, China's latest patents, Technical Efficacy Thesaurus, Application Domain, Technology Topic, Popular Technical Reports.
© 2025 PatSnap. All rights reserved.Legal|Privacy policy|Modern Slavery Act Transparency Statement|Sitemap|About US| Contact US: help@patsnap.com