Heating system for heating heat-transfer oil usingboiler flue gas
a technology of heating system and boiler flue gas, which is applied in the direction of water feed control, heating type, automatic control of ignition, etc., can solve the problems of large waste of energy, low temperature corrosion generally occurs, and high corrosion of heating surfaces, so as to ensure the efficiency and output of the original boiler, reduce the temperature of the exhaust gas of the furnace, and improve the energy utilization efficiency
- Summary
- Abstract
- Description
- Claims
- Application Information
AI Technical Summary
Benefits of technology
Problems solved by technology
Method used
Image
Examples
Embodiment Construction
[0022]A heating system of heat-transfer oil using exhaust heat of flue gas from a boiler, the system comprises an economizer 3 and an air preheater 4 being disposed inside a flue 1 along a flow direction of the flue gas. The system further comprises a heat-transfer oil heater 2 disposed inside the flue 1 in front of the economizer 3. The heat-transfer oil heater 2 is connected to a heat consumption device 19 via a first circulating pipe. A circulating pump 12 is disposed on the first circulating pipe.
[0023]As shown in FIG. 1, the heat-transfer oil heater 2, the economizer 3, and the air preheater 4 are disposed inside the flue 1 along the flow direction of the flue gas. The heat-transfer oil heater 2 is connected to the heat consumption device 19 via the first circulating pipe. The circulating pump 12 is disposed on the first circulating pipe for driving the circulation of a heat carrier of the heat-transfer oil heater 2. In a rear part of the flue 1, part of the heat energy of the ...
PUM
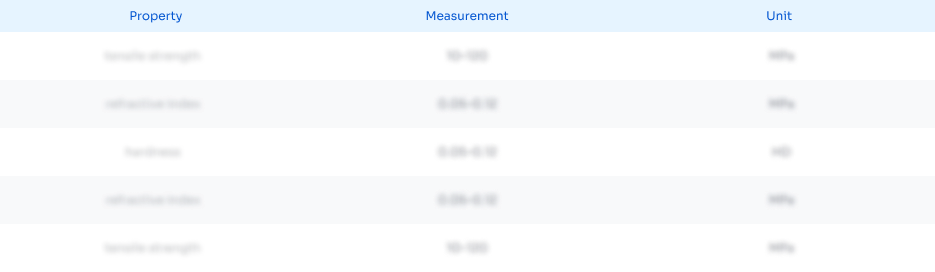
Abstract
Description
Claims
Application Information

- R&D
- Intellectual Property
- Life Sciences
- Materials
- Tech Scout
- Unparalleled Data Quality
- Higher Quality Content
- 60% Fewer Hallucinations
Browse by: Latest US Patents, China's latest patents, Technical Efficacy Thesaurus, Application Domain, Technology Topic, Popular Technical Reports.
© 2025 PatSnap. All rights reserved.Legal|Privacy policy|Modern Slavery Act Transparency Statement|Sitemap|About US| Contact US: help@patsnap.com