Method and Apparatus for Controlling Gas Turbine Combustor
a technology of gas turbine combustor and combustor body, which is applied in the direction of mechanical equipment, machines/engines, lighting and heating equipment, etc., to achieve the effect of reducing nox emission
- Summary
- Abstract
- Description
- Claims
- Application Information
AI Technical Summary
Benefits of technology
Problems solved by technology
Method used
Image
Examples
embodiment 1
[0045]The control apparatus of the gas turbine combustor and the control method of the gas turbine combustor of the first embodiment of the present invention will be explained by referring to FIGS. 1 to 3.
[0046]FIG. 1 shows an entire drawing of the gas turbine unit for power generation having the gas turbine combustor which is the first embodiment of the present invention, and the gas turbine unit includes a compressor 1, a gas turbine combustor 2, and a turbine 3, and by the output of the turbine 3, a generator 4 is rotated, thus power is obtained.
[0047]Compressed air 100 compressed by the compressor 1 flows into the gas turbine combustor 2 via a diffuser 5 and passes between an outer sleeve 6 and a combustor liner 7.
[0048]A part of the compressed air 100 flows into a combustion chamber 8 of the gas turbine combustor 2 as cooling air 101 of the combustor liner 7. The compressed air 100 not used as cooling air 101 respectively flows into a diffusion combustion burner 9 arranged on t...
embodiment 2
[0070]Next, the control apparatus of the gas turbine combustor and the control method of the gas turbine combustor of the second embodiment of the present invention will be explained by referring to FIGS. 4 and 5. The control apparatus of the gas turbine combustor 2 of the second embodiment of the present invention is the same as that of the gas turbine combustor 2 of the first embodiment shown in FIGS. 1 to 3 in the basic constitution, so that the explanation common to the two is omitted and only the different portions will be explained below.
[0071]FIG. 4 shows an entire drawing of the gas turbine unit for power generation including the gas turbine combustor 2 which is the second embodiment of the present invention and the control apparatus of the gas turbine combustor 2 of this embodiment, in addition to the constitution of the gas turbine combustor 2 of the first embodiment, is structured so as to install a rotating speed comparison arithmetic unit 204 for comparing a set switchi...
embodiment 3
[0081]Next, the control apparatus of the gas turbine combustor and the control method of the gas turbine combustor of the third embodiment of the present invention will be explained by referring to FIGS. 6 and 7. The control apparatus of the gas turbine combustor 2 of the third embodiment of the present invention is the same as that of the gas turbine combustor 2 of the first embodiment shown in FIGS. 1 to 3 in the basic constitution, so that the explanation common to the two is omitted and only the different portions will be explained below.
[0082]FIG. 6 shows an entire drawing of the gas turbine unit for power generation including the gas turbine combustor 2 which is the third embodiment of the present invention and the gas turbine combustor 2 of this embodiment, in addition to the constitution of the gas turbine combustor 2 of the first embodiment, is structured so as to install a switching rotating speed arithmetic unit 206 for calculating the rotating speed of the gas turbine to...
PUM
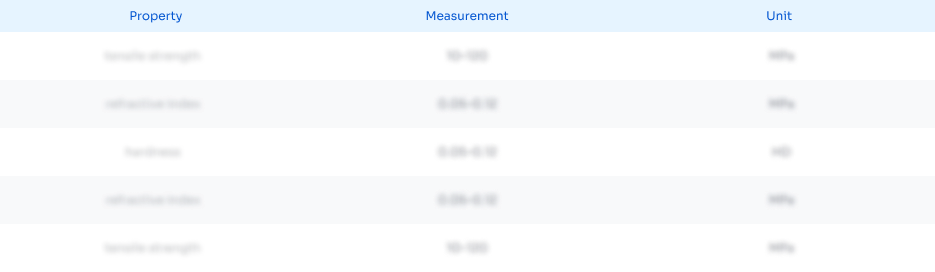
Abstract
Description
Claims
Application Information

- R&D
- Intellectual Property
- Life Sciences
- Materials
- Tech Scout
- Unparalleled Data Quality
- Higher Quality Content
- 60% Fewer Hallucinations
Browse by: Latest US Patents, China's latest patents, Technical Efficacy Thesaurus, Application Domain, Technology Topic, Popular Technical Reports.
© 2025 PatSnap. All rights reserved.Legal|Privacy policy|Modern Slavery Act Transparency Statement|Sitemap|About US| Contact US: help@patsnap.com