Fluid regulator
- Summary
- Abstract
- Description
- Claims
- Application Information
AI Technical Summary
Benefits of technology
Problems solved by technology
Method used
Image
Examples
Embodiment Construction
[0033]In FIG. 1, a schematical cross section through a first possible embodiment of a pressure regulator 1 is depicted. The pressure regulator 1 comprises a casing 2 with a fluid inlet port 3 and a fluid outlet port 4. Both fluid inlet port 3 and fluid outlet port 4 have an inner thread 5, so that a corresponding fluid pipe or fluid hose can be threadingly engaged in the respective fluid port 3, 4.
[0034]Within the casing 2 of the pressure regulator 1, a valve unit 6 is arranged. The valve unit 6 essentially consists of a valve seat 7 and a valve tube 8. The valve tube 8 can be moved in an axial direction (as indicated by double-headed arrow A) within the casing 2 of the pressure regulator 1.
[0035]The valve tube 8 is designed to have a hollow interior 9, forming an inner fluid line 9 through the valve tube 8. The contacting area between valve seat 7 and valve tube 8 forms the valve opening 10. If the valve tube 8 is in its leftmost position (as drawn in FIG. 1), the valve seat 7 and ...
PUM
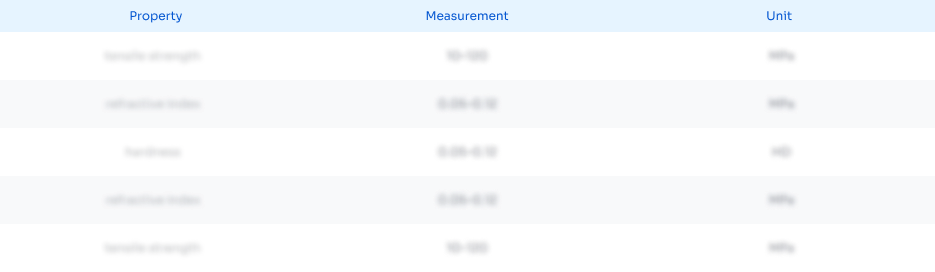
Abstract
Description
Claims
Application Information

- R&D
- Intellectual Property
- Life Sciences
- Materials
- Tech Scout
- Unparalleled Data Quality
- Higher Quality Content
- 60% Fewer Hallucinations
Browse by: Latest US Patents, China's latest patents, Technical Efficacy Thesaurus, Application Domain, Technology Topic, Popular Technical Reports.
© 2025 PatSnap. All rights reserved.Legal|Privacy policy|Modern Slavery Act Transparency Statement|Sitemap|About US| Contact US: help@patsnap.com