Method of Increasing the Performance of a Carbonaceous Fuel Combusting Boiler System
a carbonaceous fuel and boiler system technology, applied in the direction of steam engine plants, machines/engines, steam regeneration, etc., can solve the problems of significant increase of lpeco, reduced efficiency, low heat transfer coefficient, etc., and achieve the effect of increasing the power of a carbonaceous fuel combusting boiler, without substantially decreasing the thermal efficiency
- Summary
- Abstract
- Description
- Claims
- Application Information
AI Technical Summary
Benefits of technology
Problems solved by technology
Method used
Image
Examples
example 1
Air-Fired Sub-Critical PC Boiler
[0032]Below are described the main results of a calculation of the effects of the present invention in a sub-critical PC boiler with reheat, fired with lignite fuel. The arrangement of heat exchangers arranged in series in the HRA includes RH, SH, ECO, GH and LEPCO. In this example, the reference case includes steam extraction from an HPST section, which will be shut off in the new case. In the example, the low temperature feedwater is heated up by an enlarged economizer to the same temperature as in the reference case, which results in no change of evaporation duty in the furnace. The heat transfer to the combustion air at the GH is reduced due to a lowered temperature of the flue gas entering the GH. As a result, the boiler fires more fuel to compensate for the low inlet air temperature. Thus, the increased firing of fuel does not increase the total heat flux in the furnace. Due to the increased reheat steam flow, the reheat duty is increased. It is...
example 2
Air-Fired Super-Critical PC Boiler
[0035]Below are described the main results of a calculation of the effects of the present invention in an SC PC boiler, with an RH and a parallel pass HRA. Two cases, named New 1 and New 2, are analyzed, corresponding to the shutting off of one, and one and one-half, correspondingly, of two high-pressure steam extractions from the high pressure steam turbine section.
[0036]Due to shutting off of the high pressure steam extractions, the temperature of the feedwater decreases from 298° C. by 32° C. and 52° C. for the cases of New 1 and New 2, the duty of the economizer rises by 60% and 120%, respectively, but the evaporation and superheat is kept unchanged. The RH steam flow and duty increase by 7% and 14%, respectively. The gas temperature to the economizer rises due to increased firing and flue gas flow, but the temperature of the flue gas at the inlet of the GH drops due to increased economizer duty, which leads to a lowering of the air temperature ...
PUM
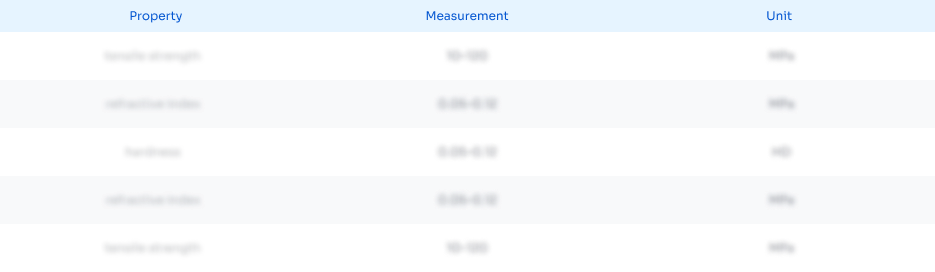
Abstract
Description
Claims
Application Information

- R&D
- Intellectual Property
- Life Sciences
- Materials
- Tech Scout
- Unparalleled Data Quality
- Higher Quality Content
- 60% Fewer Hallucinations
Browse by: Latest US Patents, China's latest patents, Technical Efficacy Thesaurus, Application Domain, Technology Topic, Popular Technical Reports.
© 2025 PatSnap. All rights reserved.Legal|Privacy policy|Modern Slavery Act Transparency Statement|Sitemap|About US| Contact US: help@patsnap.com