Control logic method and system for optimizing natural gas production
- Summary
- Abstract
- Description
- Claims
- Application Information
AI Technical Summary
Benefits of technology
Problems solved by technology
Method used
Image
Examples
Embodiment Construction
[0136]The teachings of the present invention may be best understood after first reviewing methods and apparatus taught by the previously-mentioned U.S. Pat. No. 6,991,034 and No. 7,275,599 (the entire disclosures of which are incorporated herein by reference).
[0137]FIG. 1 schematically illustrates a natural gas well W penetrating a subsurface formation F containing natural gas, with well W producing gas under velocity-induced flow conditions in accordance with one embodiment of the methods taught in U.S. Pat. No. 6,991,034. Well W is lined with a casing 20 which has a number of perforations conceptually illustrated by short lines 22 within a production zone (generally corresponding to the portion of the well penetrating the formation F). As conceptually indicated by arrows 24, formation fluids including gas, oil, and water flow into the well through perforations 22. A string of tubing 30 extends inside casing 20, terminating at a point within the production zone. The bottom end of t...
PUM
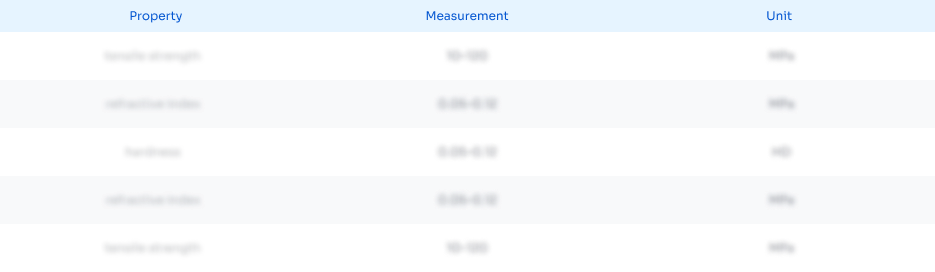
Abstract
Description
Claims
Application Information

- R&D
- Intellectual Property
- Life Sciences
- Materials
- Tech Scout
- Unparalleled Data Quality
- Higher Quality Content
- 60% Fewer Hallucinations
Browse by: Latest US Patents, China's latest patents, Technical Efficacy Thesaurus, Application Domain, Technology Topic, Popular Technical Reports.
© 2025 PatSnap. All rights reserved.Legal|Privacy policy|Modern Slavery Act Transparency Statement|Sitemap|About US| Contact US: help@patsnap.com