Drainpipe heat exchanger
a heat exchanger and drainpipe technology, applied in the direction of recuperative heat exchangers, stationary tubular conduit assemblies, heating/cooling energy-saving, etc., can solve the problems of heat exchangers, simple but expensive dhr heat exchangers, poor use of heat transfer surface area, etc., to achieve easy sliding and maximize thermal conduction
- Summary
- Abstract
- Description
- Claims
- Application Information
AI Technical Summary
Benefits of technology
Problems solved by technology
Method used
Image
Examples
Embodiment Construction
[0044]Two basic embodiments are disclosed, vertical heat exchanger 100, and horizontal heat exchanger 200. each has two conduits in thermal contact. One conduit is a straight pipe or tube that typically carries a waste fluid from which heat is to be recovered, and the second conduit is for the second fluid to which heat is to be transferred, although the heat transfer path could be reversed. Generally the conduits are metal and preferably copper if the temperature differential is small and therefore requires fast heat transfer. The two conduits are co-operatively shaped and tightly clamped together so as to provide optimal thermal contact and thus rapid heat transfer. In the horizontal embodiment the waste conduit is normally on top of the second conduit (waste fluid has heat to be recovered), while in the vertical embodiment the waste conduit is encircled by the second conduit.
[0045]One novel feature of the instant invention is the use of the internal water pressure in the colds wa...
PUM
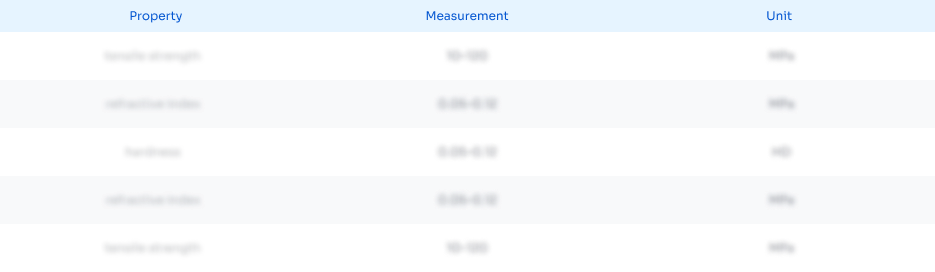
Abstract
Description
Claims
Application Information

- R&D
- Intellectual Property
- Life Sciences
- Materials
- Tech Scout
- Unparalleled Data Quality
- Higher Quality Content
- 60% Fewer Hallucinations
Browse by: Latest US Patents, China's latest patents, Technical Efficacy Thesaurus, Application Domain, Technology Topic, Popular Technical Reports.
© 2025 PatSnap. All rights reserved.Legal|Privacy policy|Modern Slavery Act Transparency Statement|Sitemap|About US| Contact US: help@patsnap.com