Combustion System and Process
a combustion system and combustion technology, applied in the field of combustion system and process, to achieve the effect of greatly reducing the nox byproduct of combustion
- Summary
- Abstract
- Description
- Claims
- Application Information
AI Technical Summary
Benefits of technology
Problems solved by technology
Method used
Image
Examples
Embodiment Construction
[0023]The system and process of the present invention involve air-staged furnace units capable of burning solid fuels. FIGS. 1-3 portray three relatively common solid fuel furnace configurations, each of which can be used in the present invention. Specifically, FIG. 1 is a schematic representation of a single wall-fired unit 10, FIG. 2 is a schematic representation of a opposed wall-fired unit 20, and FIG. 3 is a schematic representation of a tangential (or corner fired) unit 30. Each of these embodiments provides front wall 11, rear wall 13, and side walls 15 and 17. Tangential unit 30 also includes four corner walls 19.
[0024]Single wall-fired unit 10 incorporates primary burners 12, re-burn burners 14 and OFA ports 16 in front wall 11. Optionally, as shown in FIG. 1, additional OFA ports may be located in rear wall 13 of the single wall-fired unit. Opposed wall-fired unit 20 incorporates primary burners 12a, re-burn burners 14a and OFA ports 16a in front wall 11 and incorporates p...
PUM
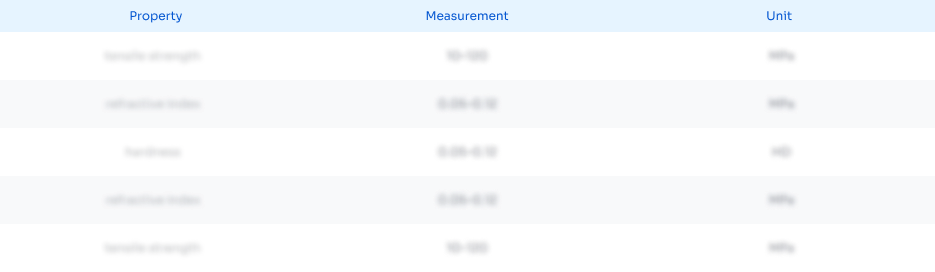
Abstract
Description
Claims
Application Information

- R&D
- Intellectual Property
- Life Sciences
- Materials
- Tech Scout
- Unparalleled Data Quality
- Higher Quality Content
- 60% Fewer Hallucinations
Browse by: Latest US Patents, China's latest patents, Technical Efficacy Thesaurus, Application Domain, Technology Topic, Popular Technical Reports.
© 2025 PatSnap. All rights reserved.Legal|Privacy policy|Modern Slavery Act Transparency Statement|Sitemap|About US| Contact US: help@patsnap.com