Substrate processing apparatus
- Summary
- Abstract
- Description
- Claims
- Application Information
AI Technical Summary
Benefits of technology
Problems solved by technology
Method used
Image
Examples
embodiment 1
[0063]Next, an explanation will be given of film fabrication examples using ALD method in regard to the case of an Al2O3 film being formed by use of TMA and O3 gases and the case of a HfO2 film being formed by using TEMAH and O3 gases, each of which cases is one of semiconductor device fabrication processes.
[0064]The ALD (Atomic Layer Deposition) method, which is one of CVD (Chemical Vapor Deposition) methods, is a technique for alternately supplying, one at a time, two (or more) kinds of raw material gases used for the film fabrication onto a wafer 200 under specified film forming conditions (temperature, time, etc.) and for causing adsorption with a one atomic layer being as a unit to thereby perform the intended film formation by utilizing surface reaction.
[0065]More specifically, in the case of forming an Al2O3 (aluminum oxide) film as an example, it is possible to form a high-quality film at low temperatures of 250 to 450° C., by alternately supplying a vaporized gas of TMA (Al...
embodiment 2
[0104]Although in the embodiment 1 there was described the case where the film formation is performed by ALD method by use of a single kind of liquid raw material for one kind of film seed, another case will be explained with reference to FIG. 7 below, which is for performing the film formation by ALD method by using three kinds of liquid raw materials. Note that members similar to those of FIG. 3 are added similar reference numerals, and detailed explanations are eliminated herein. Also note that each raw material gas supply source and its constituent members are designated by reference numerals with a character (A, B or C) being added thereto at a tail end of reference numeral, which is different from that of another raw material gas supply source and its constituent members, in order to distinguish it from the another raw material gas supply source and its constituent members.
[0105]For example, in the case of forming a SiO2 film by using a catalytic agent, HCD (hexachlorodisilane...
PUM
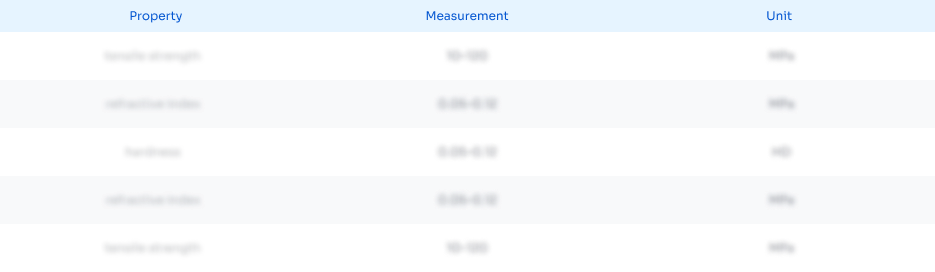
Abstract
Description
Claims
Application Information

- R&D
- Intellectual Property
- Life Sciences
- Materials
- Tech Scout
- Unparalleled Data Quality
- Higher Quality Content
- 60% Fewer Hallucinations
Browse by: Latest US Patents, China's latest patents, Technical Efficacy Thesaurus, Application Domain, Technology Topic, Popular Technical Reports.
© 2025 PatSnap. All rights reserved.Legal|Privacy policy|Modern Slavery Act Transparency Statement|Sitemap|About US| Contact US: help@patsnap.com