Process for the preparation of magnesia (MgO)
a technology of magnesia and process, applied in the field of improvement, can solve the problems of deterioration of mechanical properties (e.g., strength and volume stability), adversely affecting the properties of sintered magnesia, and high impurity content of magnesite or
- Summary
- Abstract
- Description
- Claims
- Application Information
AI Technical Summary
Benefits of technology
Problems solved by technology
Method used
Image
Examples
example 1
[0084]200 g of MgCl2.6H2O (0.985 moles) was reacted with 75.53 g of NaOH (1.890 moles). The residue obtained on filtration was washed with water. The mass of the wet cake was 270.65 g. Of this 235.34 g was dried at 110° C. to obtain 77.98 g of dry residue. 60 g of this dry residue was calcined to obtain 22.55 g MgO having>99% purity. The loss on ignition was 62.42% (theoretical LOI=30.88%). The observations from this example are that, even though MgO of high purity is obtainable, this is achieved only through elaborate and tedious washing.
example 2
[0085]250 g of MgCl2.6H2O (1.232 moles) was reacted with 190.8 g of 23.8% (w / w) ammonia solution (2.671 moles) and the slurry was stirred for 15 min and then filtered. Filtration was found to be very facile. The residue was washed with 280 mL of pure water to obtain 152 g wet cake which, on drying at 110° C. yielded a weight of 43.40 g. Of this, 31.83 g was calcined at 900° C. to give 21.13 g of MgO (58.46% yield w.r.t. MgCl2) having>99.31% purity. The loss on ignition was 33.71% (theoretical LOI=30.88%) indicating that the dried material prior to calcinations was essentially pure Mg(OH)2. This example establishes that no complexed form of ammonia exists in the product mixture and that all impurities are therefore of adhering nature. These are expected to be MgCl2, NH3 and NH4Cl besides some minor impurities, if any, which may be present in the solid MgCl2.6H2O. It will be further evident that the major adhering impurities would either be converted into MgO or volatilize away on cal...
example 3
[0086]100 gm of MgCl2.6H2O (AR grade) (0.493 moles) having available MgCl2 content of 46.8 gm was mixed under stirring with 73.44 ml (NH3=23.84% w / w; sp. Gr. 0.91)) of ammonia liquor (0.937 moles) of specific gravity 0.91. The mixture was allowed to stand for two hours. The resultant slurry could be readily filtered by vacuum filtration. Wet cake weighing 51.5 gms and 92 ml of filtrate having specific gravity of 1.12 and chemical composition Ca=ND %, Mg=2.68%, Cl=20.38% was obtained. The wet cake was washed with 50 ml water. The wash filtrate composition is, Ca=ND, Mg=0.83%, Cl=5.44%. The cake was dried at 110 C to obtain dry mass of 43.43 gm which was further calcined at 900 C to obtain 13.78 gm (0.344 moles; 70% yield) of MgO showing purity of 99.35%, CaO=ND and Cl=0.37% and B2O3=0.012%. It will be evident from this example and the powder XRD of FIG. 2 that MgO purity matching that of Example 1 is obtainable if the MgCl2 taken is free of impurity salts as is the case when AR grade...
PUM
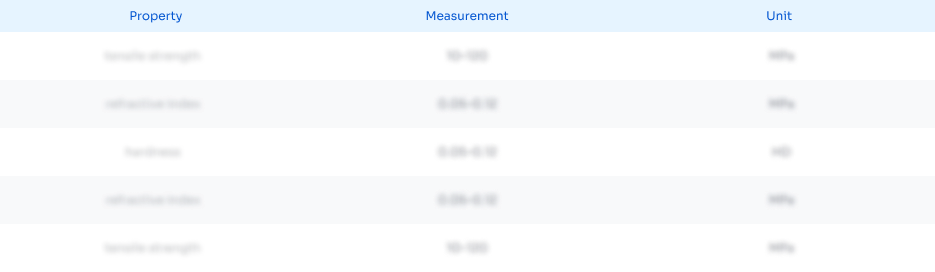
Abstract
Description
Claims
Application Information

- R&D
- Intellectual Property
- Life Sciences
- Materials
- Tech Scout
- Unparalleled Data Quality
- Higher Quality Content
- 60% Fewer Hallucinations
Browse by: Latest US Patents, China's latest patents, Technical Efficacy Thesaurus, Application Domain, Technology Topic, Popular Technical Reports.
© 2025 PatSnap. All rights reserved.Legal|Privacy policy|Modern Slavery Act Transparency Statement|Sitemap|About US| Contact US: help@patsnap.com