Commercial laundry machine with improved loading hopper
- Summary
- Abstract
- Description
- Claims
- Application Information
AI Technical Summary
Benefits of technology
Problems solved by technology
Method used
Image
Examples
Embodiment Construction
[0034] Referring now more particularly to the drawings, there is shown an illustrative commercial laundry machine 10 having a loading hopper unit 11 embodying the present invention. The laundry machine 10 includes a conventional drum 13 that is rotatably mounted within a machine housing 14 and has a front opening 15, through which launderable items are introduced into the drum 13 for laundering. As is known in the art, the housing 14 and drum 13 are adapted to be tilted relative to the horizontal between loading, laundering, and unloading positions. The illustrated laundry machine 10 further has inflatable bags 16 of a conventional type for supporting the machine in isolated relation to the floor during liquid extract cycles of operation when the machine is subjected to extensive vibrations.
[0035] For facilitating the direction and loading of launder-able items released from an overhead sling 18 into the front opening 15 of the laundry machine drum 13, the hopper unit 11 is mounted...
PUM
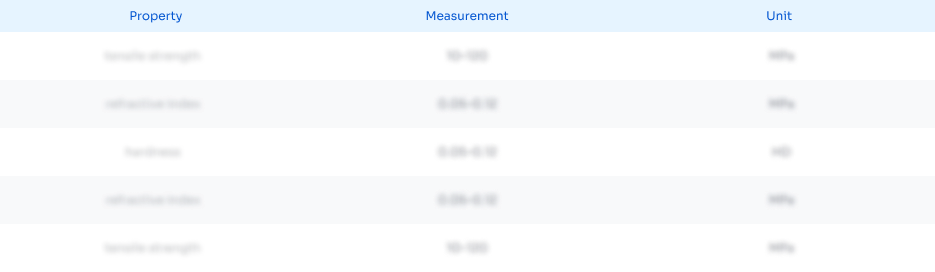
Abstract
Description
Claims
Application Information

- R&D
- Intellectual Property
- Life Sciences
- Materials
- Tech Scout
- Unparalleled Data Quality
- Higher Quality Content
- 60% Fewer Hallucinations
Browse by: Latest US Patents, China's latest patents, Technical Efficacy Thesaurus, Application Domain, Technology Topic, Popular Technical Reports.
© 2025 PatSnap. All rights reserved.Legal|Privacy policy|Modern Slavery Act Transparency Statement|Sitemap|About US| Contact US: help@patsnap.com