Cyclone core machining method
A processing method and swirl core technology, applied in the field of swirl core processing, can solve the problems of complex dimensional accuracy requirements of swirl core structure, long processing cycle and turnaround time, poor part size consistency, etc., so as to reduce the operation intensity of performance debugging , improve dimensional consistency and surface quality, and ensure the effect of machining accuracy
- Summary
- Abstract
- Description
- Claims
- Application Information
AI Technical Summary
Problems solved by technology
Method used
Image
Examples
Embodiment
[0048] (1) Take the wool of the swirl core whose length is longer than the length of the swirl core to be formed after the turning and milling clamp, and install the wool of the swirl core on the turning and milling spindle. The size of the swirl core to be formed is as follows Figure 5 As shown; this application installs a Φ10 circlip on the main shaft, and a Φ5 circlip on the sub-spindle;
[0049] (2) Turning and milling swirl core wool inner shape and drilling, see the process diagram Figure 6 :
[0050] Step 1: The main shaft clamps the wool, the flat end face, rough and fine car shape, get as follows Figure 6a Swirl core wool structure, the processing process is summarized to ensure the relevant dimensions; the tool used: 85° outer circle turning tool;
[0051] Step 2: Drill the center hole to get such as Figure 6 b swirl core wool structure, the processing process is summarized to ensure the relevant dimensions; the tool used: ф0.8 center drill;
[0052] Step 3: ...
PUM
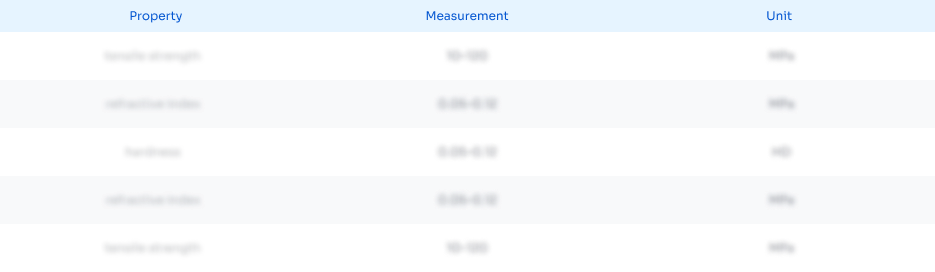
Abstract
Description
Claims
Application Information

- R&D
- Intellectual Property
- Life Sciences
- Materials
- Tech Scout
- Unparalleled Data Quality
- Higher Quality Content
- 60% Fewer Hallucinations
Browse by: Latest US Patents, China's latest patents, Technical Efficacy Thesaurus, Application Domain, Technology Topic, Popular Technical Reports.
© 2025 PatSnap. All rights reserved.Legal|Privacy policy|Modern Slavery Act Transparency Statement|Sitemap|About US| Contact US: help@patsnap.com