Process production method with multiple cast ingot heating furnaces simultaneously parallel to hot rolling direction
A production method and heating furnace technology, applied in the direction of metal rolling, etc., can solve the problems of inability to completely move out of the limit hoisting position of the hot-rolled straddle crane, restrictions on the lifting of extra-heavy ingots, and high heating temperature of ingots, and achieve shortened installation. The effect of reducing the material time, reducing the labor intensity of workers, and improving the production efficiency of hot rolling
- Summary
- Abstract
- Description
- Claims
- Application Information
AI Technical Summary
Problems solved by technology
Method used
Image
Examples
Embodiment Construction
[0026] The invention is a process production method in which several ingot heating furnaces are simultaneously parallel to the hot rolling direction.
[0027] combine figure 1 , set the hot-rolling workshop of aluminum strips to have ingot storage bay A, heating bay B, and hot-rolling bay C. Ingot storage bay A is equipped with 4 cars on the first day, hot-rolled bay C is equipped with 10 cars on the second day, and heating bay B Equipped with several ingot heating furnaces 1, material storage platform 2, composite material car 3, hot rolling roller table 6, and track 9 are all conventional equipment, ingot heating furnace 1 is composed of a rectangular box-type furnace body and a trolley, and the material storage platform 2 is used to place the ingot to be heated after milling, the composite material car 3 reciprocates on the track 9 and is used for the transportation of the ingot 5, and the hot rolling roller table 6 belongs to the auxiliary equipment of the hot rolling mil...
PUM
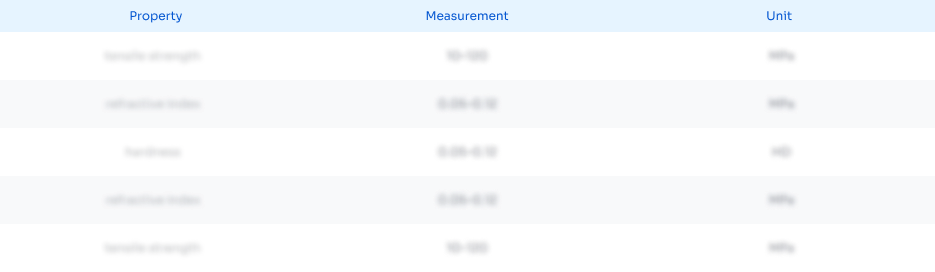
Abstract
Description
Claims
Application Information

- Generate Ideas
- Intellectual Property
- Life Sciences
- Materials
- Tech Scout
- Unparalleled Data Quality
- Higher Quality Content
- 60% Fewer Hallucinations
Browse by: Latest US Patents, China's latest patents, Technical Efficacy Thesaurus, Application Domain, Technology Topic, Popular Technical Reports.
© 2025 PatSnap. All rights reserved.Legal|Privacy policy|Modern Slavery Act Transparency Statement|Sitemap|About US| Contact US: help@patsnap.com