Polyethane conveyer belt for coal mine and its making process
A manufacturing method, polyurethane technology, applied in applications, belts, household appliances, etc., can solve problems such as low friction coefficient, fire hazard, and degradation of rubber wear resistance, and achieve simple molding process, less equipment investment, and high conveying efficiency Effect
- Summary
- Abstract
- Description
- Claims
- Application Information
AI Technical Summary
Problems solved by technology
Method used
Examples
Embodiment 1
[0028] The present invention comprises following steps and processing condition:
[0029] Step 1: Preparation of strip blank
[0030] The commonly used braided belt core impregnated with polyvinyl chloride paste and plasticized at high temperature is selected as the belt blank. Wipe the surface clean with ethyl acetate, spray or brush the adhesive prepared in patent 200510101982.4, and then it can be used for cast polyurethane conveyor belt.
[0031] Step 2: Preparation of polyurethane covering glue system
[0032] In this embodiment, the covering glue polyurethane elastomer adopts a polytetrahydrofuran diol / toluene diisocyanate system with a molecular weight of 1000, and the flame retardant adopts resorcinol bis(diphenyl phosphate) or a phosphorus flame retardant with the trade name NceydXP30 , the system was synthesized by a conventional method.
[0033] Weigh 100 parts by mass of polytetrahydrofuran diol with an average molecular weight of 1000, put it into a reaction ke...
Embodiment 2
[0040] The present invention comprises following steps and processing condition:
[0041] Step 1: Preparation of strip blank
[0042] Unwind the belt blank that has been plasticized at high temperature and coiled, wipe the surface clean with ethyl acetate, brush the same adhesive as in Example 1, and then it can be used for casting polyurethane conveyor belts.
[0043] Step 2: Preparation of polyurethane covering glue system
[0044] In this embodiment, the cover rubber polyurethane elastomer adopts the polycaprolactone diol / diphenylmethane diisocyanate system with a molecular weight of 1000, and the flame retardant adopts the halogenated flame retardant ethane 1,2 bis(pentabromobenzene) or four Bromophthalic anhydride derivatives, the system is synthesized by conventional methods.
[0045] Weigh 100 parts by mass of polycaprolactone diol with an average molecular weight of 1000, put it into a reaction kettle, heat to 120±10°C, evacuate until the residual pressure is less th...
Embodiment 3
[0052] The present invention comprises following steps and processing condition:
[0053] Step 1: Preparation of strip blank
[0054] After the belt blank is plasticized and shaped at high temperature, the surface is wiped clean with acetone, and the same adhesive as in Example 1 is sprayed, and then it can be used for casting polyurethane conveyor belt.
[0055] Step 2: Preparation of polyurethane covering glue system
[0056] In this example, the covering glue polyurethane elastomer adopts the polycaprolactone diol / toluene diisocyanate system with a molecular weight of 2000, and the flame retardant adopts phosphorus-halogen composite flame retardant PUR3 or phosphorus-based flame retardant FyrolPNX, and the system is synthesized according to a conventional method .
[0057]Weigh 100 parts by mass of polycaprolactone diol with an average molecular weight of 2000, put it into a reaction kettle, heat to 120±10°C, evacuate until the residual pressure is less than 500Pa, remove...
PUM
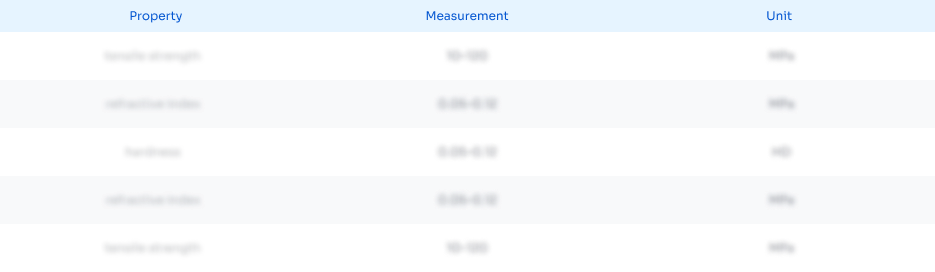
Abstract
Description
Claims
Application Information

- R&D
- Intellectual Property
- Life Sciences
- Materials
- Tech Scout
- Unparalleled Data Quality
- Higher Quality Content
- 60% Fewer Hallucinations
Browse by: Latest US Patents, China's latest patents, Technical Efficacy Thesaurus, Application Domain, Technology Topic, Popular Technical Reports.
© 2025 PatSnap. All rights reserved.Legal|Privacy policy|Modern Slavery Act Transparency Statement|Sitemap|About US| Contact US: help@patsnap.com