Method for selective laser sintering for quick and direct production of injection die
A technology of laser sintering and injection molding, applied in the direction of digital control, comprehensive factory control, electrical program control, etc., can solve the problems of high cost, difficult to control the forming process, low precision, etc., achieve low cost, short processing cycle, and widen the scope Effect
- Summary
- Abstract
- Description
- Claims
- Application Information
AI Technical Summary
Problems solved by technology
Method used
Examples
example 1
[0017] (1) Use the 3D modeling software to design the CAD 3D model of the part, then process it with the slicing software and save it as an STL file, and send the data information of the STL file to the SLS rapid prototyping machine.
[0018] (3) Lay a layer of raw powder material at the bottom of the powder bed of the selective laser sintering machine, using CO 2 Or the YAG laser scans and sinters the selected area with the laser beam guided by the information of the precise slice level. At the position where the laser is irradiated, the powder materials are sintered together. The next layer of powder is laid and sintered, and the new layer is naturally sintered with the previous layer. The laser spot diameter is 100μm, the scanning distance is 0.1mm, the scanning speed is 1500mm / s, the laser power is 15W, and the thickness of the single layer Take 100 μm and scan the composite powder.
[0019] The raw material powder is a polyamide / copper composite material, wherein the par...
example 2
[0024] (1) Use the 3D modeling software to design the CAD 3D model of the part, then process it with the slicing software and save it as an STL file, and send the data information of the STL file to the SLS rapid prototyping machine.
[0025] (2) Spread a layer of raw material powder at the bottom of the powder bed of the selective laser sintering machine, and use CO 2 Or the YAG laser scans and sinters the selected area with the laser beam guided by the information of the precise slice level. At the position where the laser is irradiated, the powder materials are sintered together. Then carry out the next layer of powder spreading and sintering. The new layer and the previous layer are naturally sintered together. The laser spot diameter is 100 μm, the scanning distance is 0.1mm, the scanning speed is 2000mm / s, the laser power is 20W, and the thickness of the single layer Take 80 μm.
[0026] The raw material powder is a polyamide / copper composite material, the particle size...
example 3
[0031] (1) Use the 3D modeling software to design the CAD 3D model of the part, then process it with the slicing software and save it as an STL file, and send the data information of the STL file to the SLS rapid prototyping machine.
[0032] (2) Lay a layer of powder material at the bottom of the powder bed of the selective laser sintering machine, using CO 2 Or the YAG laser scans and sinters the selected area with the laser beam guided by the information of the precise slice level. At the position where the laser is irradiated, the powder materials are sintered together. The next layer is powdered and sintered, and the new layer is naturally sintered with the previous layer. The laser spot diameter is 100 μm, the scanning distance is 0.1 mm, the scanning speed is 3000 mm / s, and the laser power is 25 W.
[0033] The raw material used is polyamide / copper composite material, the particle size of copper powder is -300 mesh, and the mass ratio of copper powder to polyamide powde...
PUM
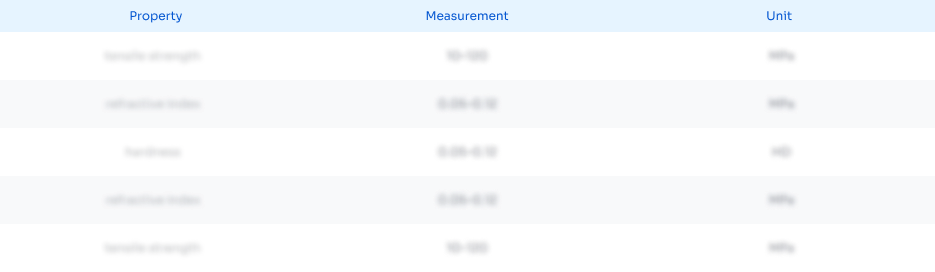
Abstract
Description
Claims
Application Information

- Generate Ideas
- Intellectual Property
- Life Sciences
- Materials
- Tech Scout
- Unparalleled Data Quality
- Higher Quality Content
- 60% Fewer Hallucinations
Browse by: Latest US Patents, China's latest patents, Technical Efficacy Thesaurus, Application Domain, Technology Topic, Popular Technical Reports.
© 2025 PatSnap. All rights reserved.Legal|Privacy policy|Modern Slavery Act Transparency Statement|Sitemap|About US| Contact US: help@patsnap.com