Production method and device for composite tube of butt welding metal tube and polymer
A production method and technology of a production device, which are applied in the field of composite pipes, can solve problems such as the weak composite of polymer and metal pipes, etc.
- Summary
- Abstract
- Description
- Claims
- Application Information
AI Technical Summary
Problems solved by technology
Method used
Image
Examples
Embodiment 1
[0050] Fig. 1-Fig. 7 has provided the figure of embodiment 1 of the present invention. Fig. 1 is a schematic structural view of a 5-layer steel-plastic composite pipe produced by the production method and device of the present invention, which are respectively inner layer polyethylene 1, inner layer adhesive layer 2, cylindrical metal pipe-steel pipe 3 from the inside to the outside , the outer adhesive layer 4, the outer polyethylene 5, and the steel pipe 3 has a butt weld 6. Also can adopt cross-linked polyethylene inner layer 7 as shown in Figure 2 inner layer. Also can adopt inner layer 8 of copolymerization polypropylene as shown in Figure 3. Alternatively, as shown in FIG. 4, the inner layer is made of cross-linked polyethylene inner layer 7, and at the same time, an oxygen barrier and anti-corrosion epoxy resin layer 9 is added on the inner and outer surfaces of the steel pipe.
[0051] Referring to Fig. 5 and Fig. 6, an unwinding machine 11 for steel strip 10, a butt...
Embodiment 2
[0054] Fig. 5, Fig. 6, Fig. 8 have provided embodiment 2 figure of the present invention. Embodiment 2 is basically the same as Embodiment 1. The difference is that as shown in Figure 8, the adhesive layer 35 on the inner and outer surfaces of the cylindrical metal frame is to pass the adhesive powder 44 through the orifice on the cylindrical frame 3 through the electrostatic powder spraying device 43 arranged on the outer periphery of the metal cylindrical frame. 45 is formed on the inner and outer surfaces of the cylindrical metal skeleton, and the electrostatic generator 46 makes the electrostatically charged binder powder 44 adhere to the inner and outer surfaces of the metal skeleton more evenly and firmly. After the electrostatic powder spraying device 43, a cylindrical skeleton heater is arranged 21. The thickness of the binder can be increased so that the binder can better melt and coat the skeleton. At the same time, the preheating ability of the skeleton can be incre...
Embodiment 3
[0056] Fig. 5, Fig. 6, Fig. 9 have provided embodiment 3 figure of the present invention. Embodiment 3 is basically the same as Embodiment 1. The difference is that as shown in Figure 6, the extrusion die head 48 extending into the welded cylindrical metal skeleton 3 has a core layer tube 34 extrusion flow channel 50 and an adhesive layer 35 extrusion flow channel respectively. 49. Under the action of the repair ring 51 (or scraper), the adhesive layer 35 extruded earlier will be close to the inner surface of the metal skeleton, and then the core layer tube 34 will be extruded, and the inner sizing rod 47 (or plugged ) under the action, the core tube 34 is compounded on the inner surface of the metal skeleton through the adhesive layer 35. The step-by-step method is used to extrude the adhesive layer separately on the inner surface of the metal skeleton, and then extrude the core layer tube on the adhesive layer, which is beneficial to separately adjust the wall thickness and...
PUM
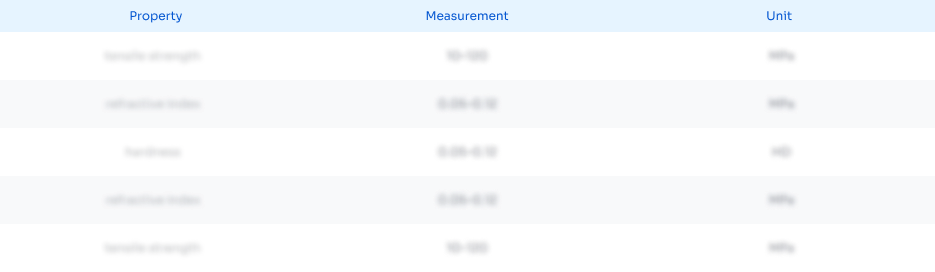
Abstract
Description
Claims
Application Information

- R&D
- Intellectual Property
- Life Sciences
- Materials
- Tech Scout
- Unparalleled Data Quality
- Higher Quality Content
- 60% Fewer Hallucinations
Browse by: Latest US Patents, China's latest patents, Technical Efficacy Thesaurus, Application Domain, Technology Topic, Popular Technical Reports.
© 2025 PatSnap. All rights reserved.Legal|Privacy policy|Modern Slavery Act Transparency Statement|Sitemap|About US| Contact US: help@patsnap.com