Preparation method and equipment of color carbon-base film
A carbon-based, thin-film technology, applied in ion implantation plating, metal material coating process, coating, etc., can solve the problems of poor film thickness and color uniformity, complicated process, harsh reaction conditions, etc., to achieve film The layer thickness and color are uniform, the process control is simple, and the effect of eliminating shadow effect
- Summary
- Abstract
- Description
- Claims
- Application Information
AI Technical Summary
Problems solved by technology
Method used
Image
Examples
Embodiment 1
[0021] Embodiment 1. Utilize above-mentioned reaction coating device to coat brown film on workpiece
[0022] Place the cleaned workpiece and the sputtered graphite target in the coating chamber of the reactive coating device, and evacuate to ≤6×10 -3 Pa, heat the coating chamber to T≥60°C, introduce inert gas argon into the coating chamber through a gas flow meter, and adjust and control the pressure in the coating chamber to 3×10 -1 Pa; connect the power supply of magnetron sputtering target 1, adjust the sputtering target current to be 3A, ionize argon, introduce reaction gas methane and nitrogen through the gas flowmeter at the same time, control the concentration of methane to be 15% and the concentration of nitrogen to be 30 %, the control reaction temperature is 80°C. Under these conditions, react for 20 minutes to obtain a workpiece coated with a brown film on the surface.
Embodiment 2
[0023] Embodiment 2. Utilize above-mentioned reaction coating device to plate gray thin film on workpiece
[0024] Place the cleaned workpiece and the sputtered graphite target in the coating chamber of the reaction coating device, and evacuate to ≤5×10 -3 Pa, heat the coating chamber to T≥60°C, introduce inert gas argon into the coating chamber through a gas flow meter, and adjust and control the pressure in the coating chamber to 2.6×10 -1 Pa. Turn on the power supply of the magnetron sputtering target 1, adjust the sputtering current to 5A, ionize the argon gas, and introduce the reaction gas ethylene and acetylene through the gas flow meter at the same time, control the concentration of ethylene to 20%, and the concentration of acetylene to 20%, to control the reaction The temperature was 200°C, and the reaction was carried out for 60 minutes under this condition, and a gray film was obtained on the surface of the workpiece.
Embodiment 3
[0025] Embodiment 3. Utilize above-mentioned reaction coating device to coat black thin film on workpiece
[0026] After cleaning, place the workpiece and the sputtering graphite target in the coating chamber of the reaction coating device, and evacuate to ≤3×10 -3 , heat the coating chamber to T≥150°C, introduce inert gas argon into the coating chamber through a gas flow meter, and adjust and control the pressure in the coating chamber to 2×10 -1 Pa. Turn on the power supply of the magnetron sputtering target 1, adjust the sputtering current to 10A, ionize argon, and introduce reaction gases methane and acetylene through the gas flow meter at the same time, control the concentration of methane to 30%, and the concentration of acetylene to 40%. Control the reaction temperature to 250° C., and react under this condition for 120 minutes to obtain a black film on the surface of the workpiece.
[0027] It can be seen from the above experiments that changing the ratio of the reac...
PUM
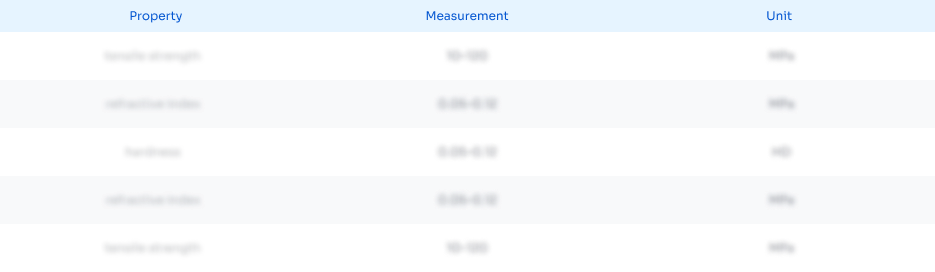
Abstract
Description
Claims
Application Information

- R&D
- Intellectual Property
- Life Sciences
- Materials
- Tech Scout
- Unparalleled Data Quality
- Higher Quality Content
- 60% Fewer Hallucinations
Browse by: Latest US Patents, China's latest patents, Technical Efficacy Thesaurus, Application Domain, Technology Topic, Popular Technical Reports.
© 2025 PatSnap. All rights reserved.Legal|Privacy policy|Modern Slavery Act Transparency Statement|Sitemap|About US| Contact US: help@patsnap.com