Homogenization treatment process of SAE8620 carburizing steel
A technology of normalizing heat treatment and carburizing steel, applied in heat treatment equipment, heat treatment process control, manufacturing tools, etc., can solve the problems of high cost and complicated process, and achieve the effect of reducing processing cost and simple process
- Summary
- Abstract
- Description
- Claims
- Application Information
AI Technical Summary
Problems solved by technology
Method used
Image
Examples
Embodiment 1
[0025] Example 1: put the billet made of SAE8620 steel into a continuous push rod furnace with a furnace temperature of 890°C, heat the billet to 890°C, keep it in the furnace for 1 hour, then raise the temperature to 910°C, and put it in the furnace After keeping warm for 2 hours, open the whole basket to air cool for 2 minutes, immediately close the whole basket and air cool for 2 minutes, then immediately put the steel into a continuous pusher furnace with a furnace temperature of 620°C, heat it to 620°C, hold it for 3 hours, and take it out of the oven. The basket is air-cooled, and the hardness can be 156HBS-207HBS (measured by the metal Brinell hardness test method stipulated in the national standard GB231-84), and the metallographic structure (as shown in Figure 2) is ferrite plus flaky pearlite, no Bainite Body machining with normalizing material.
Embodiment 2
[0026] Example 2: put the billet made of SAE8620 steel into a continuous push rod furnace with a furnace temperature of 880°C, heat the billet to 880°C, keep it in the furnace for 2 hours, then raise the temperature to 920°C, and put it in the furnace After keeping warm for 3 hours, open the whole basket to air cool for 3 minutes, immediately close the whole basket and air cool for 2 minutes, then immediately put the steel into a continuous pusher furnace with a furnace temperature of 640°C, heat it to 640°C, hold it for 4 hours, and take it out of the oven. The basket is air-cooled, and the hardness can be 156HBS-207HBS (measured by the metal Brinell hardness test method stipulated in the national standard GB231-84), and the metallographic structure (as shown in Figure 2) is ferrite plus flaky pearlite, no Bainite Body machining with normalizing material.
Embodiment 3
[0027] Example 3: Put the billet made of SAE8620 steel into a continuous push rod furnace with a temperature of 910°C in the furnace, heat the billet to 910°C, keep it in the furnace for 1 hour, and then raise the temperature to 930°C. After keeping warm for 2 hours, open the whole basket to air cool for 2 minutes, immediately close the whole basket and air cool for 3 minutes, then immediately put the steel into a continuous pusher furnace with a furnace temperature of 650°C, heat it to 650°C, hold it for 2 hours, and take it out of the oven. The basket is air-cooled, and the hardness can be 156HBS-207HBS (measured by the metal Brinell hardness test method stipulated in the national standard GB231-84), and the metallographic structure (as shown in Figure 2) is ferrite plus flaky pearlite, no Bainite Body machining with normalizing material.
PUM
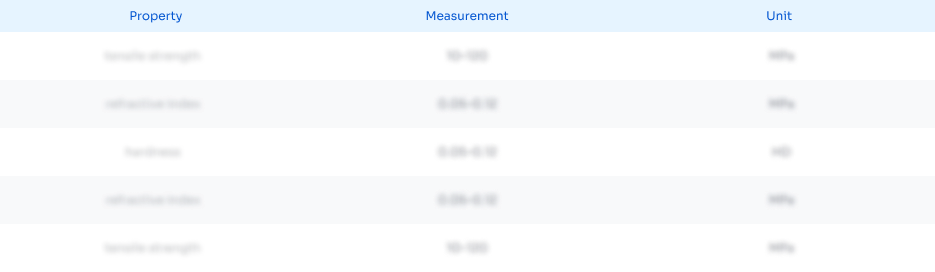
Abstract
Description
Claims
Application Information

- R&D Engineer
- R&D Manager
- IP Professional
- Industry Leading Data Capabilities
- Powerful AI technology
- Patent DNA Extraction
Browse by: Latest US Patents, China's latest patents, Technical Efficacy Thesaurus, Application Domain, Technology Topic, Popular Technical Reports.
© 2024 PatSnap. All rights reserved.Legal|Privacy policy|Modern Slavery Act Transparency Statement|Sitemap|About US| Contact US: help@patsnap.com