Preparation method of nylon/montmorillonoid fire retarding composite material
A flame retardant composite material and montmorillonite technology, which is applied in the field of polymer/montmorillonite composite material preparation, can solve the problems of application limitation, toxic gas release, large addition amount, etc., and achieves improved notched impact strength, limited oxygen The effect of exponentially increasing and easily controllable conditions
- Summary
- Abstract
- Description
- Claims
- Application Information
AI Technical Summary
Problems solved by technology
Method used
Examples
Embodiment 1
[0019] First add 2 parts of hydroxyalkyl silicone oil to 10 parts of acetone solvent at a temperature of 10°C. After stirring and dispersing evenly, add 5 parts of organic montmorillonite, continue stirring for 2 minutes, and then put it in a blast oven at 80°C The organic montmorillonite modified by silicone oil was obtained by drying at the bottom.
[0020] Mix the prepared silicone oil-modified organomontmorillonite and 100 parts of nylon 6 evenly in a high-speed mixer, then put them into a twin-screw extruder, extrude and granulate at a temperature of 180-260°C, and obtain Nylon / montmorillonite flame retardant composite.
Embodiment 2
[0022] First add 4 parts of aminohydrocarbon-based silicone oil to 40 parts of ethanol solvent at a temperature of 30°C. After stirring and dispersing evenly, add 5 parts of organic montmorillonite, continue stirring for 15 minutes, and then put it in a blast oven at 80°C. The organic montmorillonite modified by silicone oil was obtained by drying at the bottom.
[0023] Mix the prepared silicone oil-modified organomontmorillonite and 100 parts of nylon 66 evenly in a high-speed mixer, then put them into a twin-screw extruder, extrude and granulate at a temperature of 180-280°C, and obtain Nylon / montmorillonite flame retardant composite.
Embodiment 3
[0025] First add 6 parts of aminohydrocarbon-based silicone oil to 150 parts of ethanol solvent at a temperature of 40°C. After stirring and dispersing evenly, add 8 parts of organic montmorillonite and continue stirring for 10 minutes. After filtering the mixture, the organic montmorillonite is dried. That is, silicone oil modified organic montmorillonite was obtained.
[0026] Mix the prepared silicone oil-modified organomontmorillonite, 80 parts of nylon 6 and 20 parts of magnesium hydroxide in a high-speed mixer, then put them into a twin-screw extruder, and extrude at a temperature of 180-260 ° C. After granulation, the nylon / montmorillonite flame-retardant composite material is obtained. Silicone oil modified organic montmorillonite can be obtained.
PUM
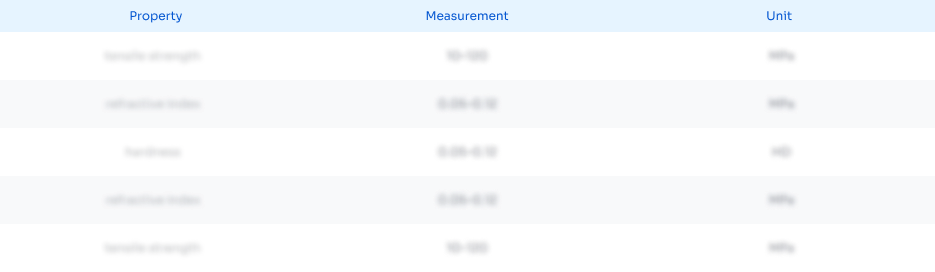
Abstract
Description
Claims
Application Information

- R&D
- Intellectual Property
- Life Sciences
- Materials
- Tech Scout
- Unparalleled Data Quality
- Higher Quality Content
- 60% Fewer Hallucinations
Browse by: Latest US Patents, China's latest patents, Technical Efficacy Thesaurus, Application Domain, Technology Topic, Popular Technical Reports.
© 2025 PatSnap. All rights reserved.Legal|Privacy policy|Modern Slavery Act Transparency Statement|Sitemap|About US| Contact US: help@patsnap.com