Optical mask pattern correcting method and its formation
A correction method and a technology of photomasks, which are applied in the direction of the original for photomechanical processing, the photoplate process of the pattern surface, optics, etc., can solve the uncontrollable, different, and affect the process yield and reliability component performance, etc. problem, to improve process yield and reliability, and save process cost
- Summary
- Abstract
- Description
- Claims
- Application Information
AI Technical Summary
Problems solved by technology
Method used
Image
Examples
Embodiment Construction
[0021] FIG. 1 is a flowchart of steps of a method for forming a photomask pattern according to an embodiment of the present invention.
[0022] Referring to FIG. 1 , in step 100 , a test photomask is provided, and a plurality of original patterns have been formed on the test photomask according to an original drawing data. For example, the original drawing data of the originally designed circuit layout pattern is written on a test photomask to form a plurality of original patterns on the test photomask. The above-mentioned original drawing data includes key dimensions, pattern density, and line width-to-spacing ratio (Duty Ratio) of the originally designed circuit layout pattern.
[0023] Step 110 , transferring the original pattern on the test photomask to the photoresist layer, so as to form a plurality of developed patterns in the photoresist layer, and measure the critical dimension of each developed pattern. Wherein, the method of transferring the original pattern on the...
PUM
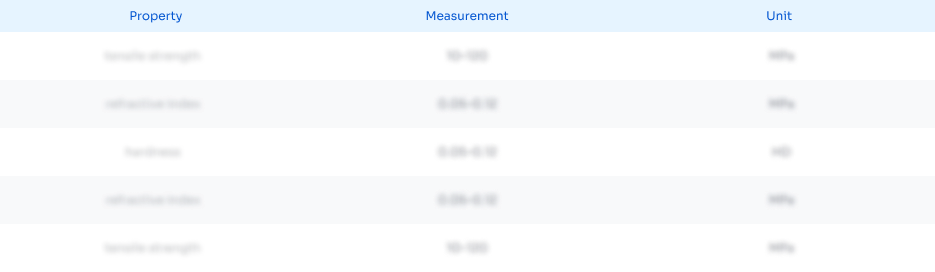
Abstract
Description
Claims
Application Information

- Generate Ideas
- Intellectual Property
- Life Sciences
- Materials
- Tech Scout
- Unparalleled Data Quality
- Higher Quality Content
- 60% Fewer Hallucinations
Browse by: Latest US Patents, China's latest patents, Technical Efficacy Thesaurus, Application Domain, Technology Topic, Popular Technical Reports.
© 2025 PatSnap. All rights reserved.Legal|Privacy policy|Modern Slavery Act Transparency Statement|Sitemap|About US| Contact US: help@patsnap.com