Compositely circulating high temperature gasifying process for making synthetic gas with biomass
A composite cycle and process method technology, which is applied in the field of composite cycle high temperature gasification technology, can solve the problems of difficulty in crushing biomass raw materials and reduce the amount of production, and achieve the effects of increasing the amount, reducing the amount of CO2 production, and high scalability.
- Summary
- Abstract
- Description
- Claims
- Application Information
AI Technical Summary
Problems solved by technology
Method used
Image
Examples
Embodiment 1
[0054] Element
[0055] The low calorific value is 11.6MJ / kg, and the ash melting point (FT) is 1250°C. The oxidant 35 uses 95% vol of oxygen to preliminarily crush the biomass raw material and dry the moisture to 5.8% before sending it into the feed bin 2. The biomass entering the low-temperature carbonization device 4 in the feed bin is controlled at 3.87kg / s, and the low-temperature The temperature rise rate of the carbonization device 4 is controlled at 0.1°C / s, the carbonization temperature is controlled at 300°C, and the pressure is controlled at 3.1MPa. 80% (approximately 6.4 MJ / s) of the heat is provided by the syngas recycle 6, which has a temperature of 600°C. The total amount of pyrolysis gas produced by the low-temperature carbonization device 4 is 3.14kg / s, and the main component of the pyrolysis gas is: H 2 7.4%, CO 33.3%, CO 2 14.2%, CH 4 7.4%, H 2 O 28.4%, N 2 1.5%, C n h m 7.8%. The pyrolysis gas enters the burner 14 of the high-tempera...
Embodiment 2
[0057] Still using the cotton stalk used in Example 1 as the biomass raw material, the biomass entering the low-temperature carbonization device 4 from the feed bin 2 is controlled at 3.87kg / s, and the temperature rise rate of the low-temperature carbonization device 4 is controlled at 1° C. / second , the heating temperature is controlled at 500°C, the pressure is controlled at 3.1MPa, and the self-heating heat of the low-temperature carbonization device 4 is controlled to be 30% (about 2.4MJ / s) of the total heat, and the remaining 70% (about 5.6MJ / s) of heat is synthesized The gas recycle 6 is provided, and the temperature of the recycle syngas 6 is 800°C. The main components of pyrolysis gas are: H 2 6.1%, CO 30.8%, CO 2 15.7%, CH 4 7.1%, H 2 O 29.2%, N 2 1.6%, C n h m 9.4%. The pyrolysis gas and the oxidant undergo an incomplete combustion reaction in the combustion zone 14, and the average temperature of the reaction is 1800°C. The charcoal is made into 150μm c...
Embodiment 3
[0059] Still using the cotton stalk used in Example 1 as the biomass raw material, the biomass entering the low-temperature carbonization device 4 from the feed bin 2 is controlled at 3.87kg / s, and the temperature rise rate of the low-temperature carbonization device 4 is controlled at 0.5°C / s , the carbonization temperature is controlled at 400°C, the pressure is controlled at 3.1MPa, the self-heating heat of the low-temperature carbonization device 4 is controlled to be 25% (about 2MJ / s) of the total heat, and the remaining 70% (about 6MJ / s) of heat is regenerated by the syngas Cycle 6 provides, recycle syngas 6 at a temperature of 700°C. The main components of pyrolysis gas are: H 2 7.2%, CO 32.3%, CO 2 15.2%, CH 4 7.2%, H 2 O 28.9%, N 2 1.6%, C n hm 7.5%. The pyrolysis gas and the oxidant undergo an incomplete combustion reaction in the combustion zone 14, and the average temperature of the reaction is 1300°C. Charcoal is made into 30 μm carbon-containing powde...
PUM
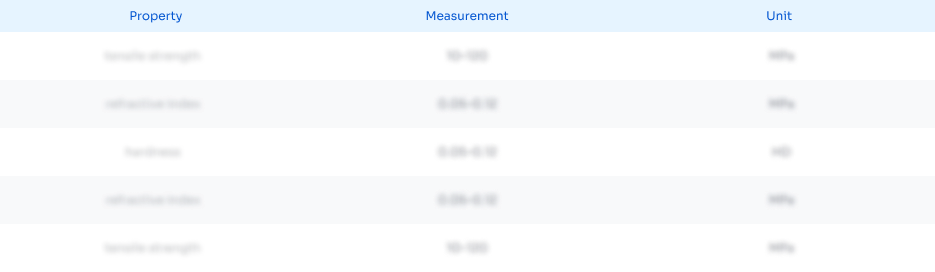
Abstract
Description
Claims
Application Information

- Generate Ideas
- Intellectual Property
- Life Sciences
- Materials
- Tech Scout
- Unparalleled Data Quality
- Higher Quality Content
- 60% Fewer Hallucinations
Browse by: Latest US Patents, China's latest patents, Technical Efficacy Thesaurus, Application Domain, Technology Topic, Popular Technical Reports.
© 2025 PatSnap. All rights reserved.Legal|Privacy policy|Modern Slavery Act Transparency Statement|Sitemap|About US| Contact US: help@patsnap.com