Nanometer composite nylon-6/inorganic particle/glass fiber and its direct prepn process
A nanocomposite material and glass fiber technology, which is applied in the field of nylon 6/inorganic particle nanocomposite and its preparation, can solve the problems of unindustrialized products and less research on nylon 6/inorganic particle/glass fiber nanocomposite, and achieve Easy nucleation, excellent orientation mechanical properties, white appearance effect
- Summary
- Abstract
- Description
- Claims
- Application Information
AI Technical Summary
Problems solved by technology
Method used
Examples
Embodiment 1
[0012] Nylon 6 / SiO 2 / Preparation of glass fiber nanocomposites
[0013] 900 g Nylon 6 / SiO 2 nanocomposite (SiO 2 content is 3%) and 100 grams of glass fibers are fully mixed in a high-speed mixer and then put into a twin-screw compounding extruder (SJSH-30 type, screw diameter 30mm, length-to-diameter ratio is 23, Nanjing Rubber Machinery Factory) for melting machinery Blending, the temperature of the five zones is: 215, 220, 225, 230, 225 ° C, the temperature of the head and the melt are 220 and 229 ° C respectively, the extrusion speed is 40prm, high-purity nitrogen protection, the molten mixture is extruded, Nylon 6 / SiO with a glass fiber content of 10% is obtained after underwater drawing, cooling, and pelletizing 2 / Glass fiber nanocomposites.
Embodiment 2
[0015] Nylon 6 / SiO 2 / Preparation of glass fiber nanocomposites
[0016] Add 11.3ml of tetraethyl orthosilicate to the reaction device, then add 3.6ml of water and 5ml of acetone, add 1 drop of 1M hydrochloric acid to adjust its acidity under stirring, hydrolyze at room temperature to obtain a transparent solution, and then add 392 grams of caprolactam Melt at a temperature of 70-80°C. After the caprolactam is completely melted, stir vigorously to mix the two evenly, and reduce pressure at the same time to extract the ethanol generated by hydrolysis and the added acetone. Add 4 grams of glass fiber, stir evenly, and then gel the resulting solution at 100-140° C. for 6 hours under the protection of high-purity nitrogen until the original uniform and transparent solution becomes a solidified transparent gel. Under the protection of high-purity nitrogen, polymerize the gel under normal pressure at 250-260°C for 15 hours, then close the nitrogen filling port, and poly...
Embodiment 3
[0018] Nylon 6 / TiO 2 / Preparation of glass fiber nanocomposites
[0019] Add 720ml of ethyl orthotitanate and 180ml of H 2 O, 180ml of acetone, hydrolyzed at room temperature to obtain a transparent solution, add 3700g of caprolactam and melt at a temperature of 70-80°C, then slowly add the hydrolyzed solution into the melted caprolactam under stirring, stir vigorously to mix the two Uniform, and then reduce the pressure at a vacuum of 0.08MPa for 20 minutes, and extract the ethanol generated by hydrolysis and the added acetone. Add 100 grams of glass fiber, stir evenly, then gel the resulting solution at 100-140°C for 6 hours under the protection of high-purity nitrogen, and gel at 250-260°C under the protection of high-purity nitrogen, 1-5 atm Under high pressure polymerization for 15 hours, then turn off the nitrogen filling port and polymerize for 8 hours under a vacuum of 0.08MPa. After purification, nylon 6 / TiO 2 / Glass fiber nanocomposite material (the t...
PUM
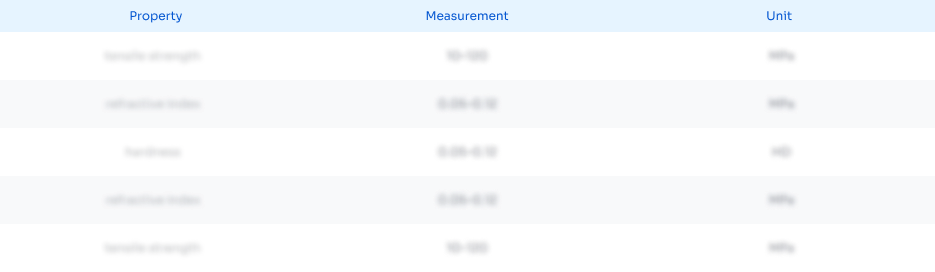
Abstract
Description
Claims
Application Information

- R&D Engineer
- R&D Manager
- IP Professional
- Industry Leading Data Capabilities
- Powerful AI technology
- Patent DNA Extraction
Browse by: Latest US Patents, China's latest patents, Technical Efficacy Thesaurus, Application Domain, Technology Topic, Popular Technical Reports.
© 2024 PatSnap. All rights reserved.Legal|Privacy policy|Modern Slavery Act Transparency Statement|Sitemap|About US| Contact US: help@patsnap.com