Method of extracting high-purity glucose from saccharified glucose syrup
A glucose syrup and glucose technology, which is applied in the direction of glucose production, sugar production, sugar production, etc., can solve the problems of impact, poor quality of filtrate, and poor glucose purification effect, so as to simplify the process, reduce operating costs, The effect of high degree of automation
- Summary
- Abstract
- Description
- Claims
- Application Information
AI Technical Summary
Problems solved by technology
Method used
Image
Examples
Embodiment 1
[0018] In Figure 1, the glucose syrup with a DE value of 92% is obtained after starch milk sizing, liquefaction, and saccharification; then after filtration, decolorization, and handover processes, it is evaporated to 60% of the dry matter; after degassing, the Enter the simulated moving bed chromatographic separation system for chromatographic separation. The conditions for chromatographic separation are: separation temperature 70°C, system pressure 1.1Mpa, feed flow rate 35ml / min, eluent flow rate 80ml / min.
[0019] After separation, the part of glucose with a glucose content of 99.3% is evaporated and crystallized to produce crystalline glucose; the part of oligosaccharides with a polysaccharide content of 70% is partly made into maltose syrup and partly returned to the saccharification process.
Embodiment 2
[0021] In Figure 1, the DE value of 94% glucose solution obtained after starch milk slurrying and liquefaction; then filtered, decolorized, separated, and evaporated to 65% dry matter; after degassing, enter the simulated moving bed chromatography at 75 ° C The separation system performs chromatographic separation, and the conditions for chromatographic separation are: separation temperature 75°C, system pressure 1.0Mpa, feed flow rate 40ml / min, eluent flow rate 100ml / min.
[0022] The part of glucose obtained after separation with a glucose content of 99.5% is evaporated and then hydrogenated to produce sorbitol; the part of oligosaccharides with a polysaccharide content of 70% is partly produced into maltose syrup and partly returned to the saccharification liquid process.
Embodiment 3
[0024] In Fig. 1, the glucose solution with a DE value of 96% obtained after sizing and liquefaction of starch milk is then filtered, decolorized, separated, and evaporated to a dry matter of 70%; after degassing, it enters the simulated moving bed chromatography at 80°C The separation system performs chromatographic separation, and the conditions for chromatographic separation are: separation temperature 80°C, system pressure 0.9Mpa, feed flow rate 30ml / min, eluent flow rate 120ml / min.
[0025] After separation, the oligosaccharide part with a polysaccharide content of 70% is partly prepared into maltose syrup, and partly returned to the saccharification liquid process. The obtained glucose portion with a glucose content of 99.8% is isomerized, crystallized after separation, decolorization, degassing, chromatographic separation, multi-effect falling film evaporation, and vacuum scraper evaporation, and then separated and dried to obtain crystalline fructose.
PUM
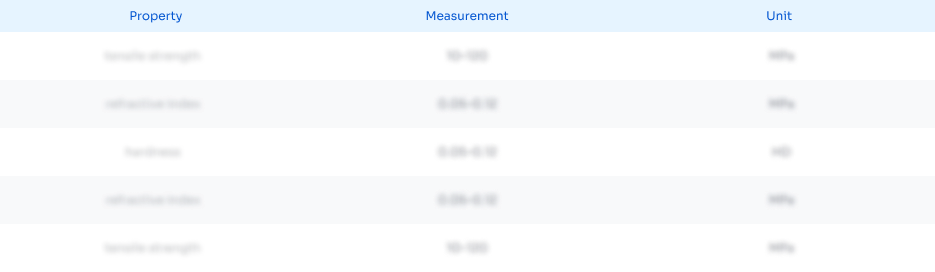
Abstract
Description
Claims
Application Information

- R&D
- Intellectual Property
- Life Sciences
- Materials
- Tech Scout
- Unparalleled Data Quality
- Higher Quality Content
- 60% Fewer Hallucinations
Browse by: Latest US Patents, China's latest patents, Technical Efficacy Thesaurus, Application Domain, Technology Topic, Popular Technical Reports.
© 2025 PatSnap. All rights reserved.Legal|Privacy policy|Modern Slavery Act Transparency Statement|Sitemap|About US| Contact US: help@patsnap.com