Method for producing biological diesel oil through homogeneous successive reaction
A biodiesel and oil technology, applied in the preparation of biological raw materials, biofuels, liquid hydrocarbon mixtures, etc., can solve the problems of difficult industrialized production, few continuous productions, harsh reaction conditions, etc., to enhance mutual solubility and shorten the Reaction time, effect of lowering reaction temperature
- Summary
- Abstract
- Description
- Claims
- Application Information
AI Technical Summary
Problems solved by technology
Method used
Image
Examples
Embodiment 1
[0031] Mix natural oil or frying waste oil, methanol, alkali metal hydroxide as a catalyst, and an organic solvent that can make the mixed liquid form a homogeneous phase, and send it to a preheater at a temperature of 30-90°C, and preheat for 1-20°C. 30 minutes, making it completely miscible to form a homogeneous system, wherein the organic solvent is one or more mixtures of ethers and ketones, or a mixture of at least one ethers and / or ketones and at least one saturated alkane The mixture, the ethers and ketones are stable to acids and alkalis and have a boiling point below 150°C, saturated alkanes have between 6 and 9 carbon atoms and a boiling point below 150°C, and the volume ratio of methanol and oil is 0.24 to 2: 1. Organic solvent volume / grease weight = 0.1L-4L / kg, the amount of catalyst alkali metal hydroxide accounts for 0.3%-2% of the grease weight; the mixed liquid is sent into the pipeline at a temperature of 40-90°C from the preheater The reactor is used for cont...
Embodiment 2
[0035]Firstly, the tube type preheater is preheated to 45°C, and the tube type reactor heating furnace is heated to 65°C. Water content is 0.1% soybean oil, methyl alcohol, tetrahydrofuran (by volume ratio 1: 1.2: 0.7) and the sodium hydroxide that accounts for soybean oil weight 0.7% is pumped into pipeline preheater, and flow velocity is 840ml / hr. After being preheated in the preheater for 2 minutes, the mixed solution enters the pipeline reactor, a temperature gradient is formed between the preheater and the reactor, and after being fully mixed and reacted for 5 minutes, it enters the distillation tower. Tetrahydrofuran and remaining methanol can be separated by distilling the mixed solution at a vacuum degree of 0-0.5 MPa, and returning to the feed pump for recycling after condensation. The still liquid enters the product separation tank and stands still, and biodiesel and crude glycerin products can be separated, and the yield of biodiesel is 97%.
Embodiment 3
[0037] Firstly, the tube type preheater is preheated to 35°C, and the tube type reactor heating furnace is heated to 62°C. Then the oil acid value is 8, the water content is 0.8% salad frying waste oil, methyl alcohol, isopropyl ether (by volume ratio 1: 1.7: 1.5) and the potassium hydroxide that accounts for salad frying waste oil weight 1.8% is pumped into Pipeline preheater with a flow rate of 620ml / hr. After being preheated in the preheater for 3 minutes, the mixed solution enters the pipeline reactor, a temperature gradient is formed between the preheater and the reactor, and after being fully mixed and reacted for 7 minutes, it enters the distillation tower. The isopropyl ether and residual methanol can be separated by distilling the mixed liquid, which is condensed and returned to the feed pump for recycling. The still liquid enters the product separation tank and stands still, and biodiesel and crude glycerin products can be separated, and the yield of biodiesel is 91...
PUM
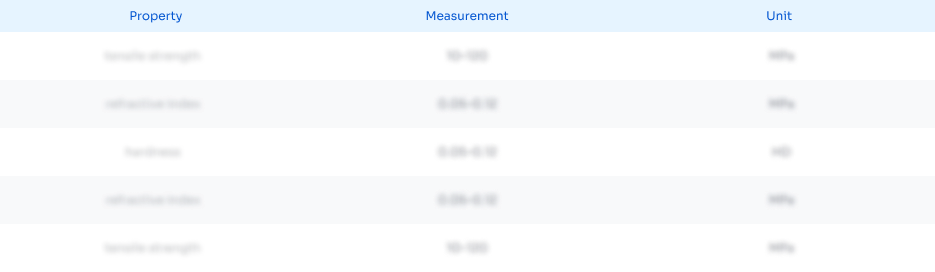
Abstract
Description
Claims
Application Information

- R&D
- Intellectual Property
- Life Sciences
- Materials
- Tech Scout
- Unparalleled Data Quality
- Higher Quality Content
- 60% Fewer Hallucinations
Browse by: Latest US Patents, China's latest patents, Technical Efficacy Thesaurus, Application Domain, Technology Topic, Popular Technical Reports.
© 2025 PatSnap. All rights reserved.Legal|Privacy policy|Modern Slavery Act Transparency Statement|Sitemap|About US| Contact US: help@patsnap.com