Fire-proof sound insulation shock-proof plate and its producing method
A technology of fire-proof, sound-proof and anti-seismic panels, which is applied in the field of building materials, can solve the problems of wasting time and manpower, time and effort, and high material costs
- Summary
- Abstract
- Description
- Claims
- Application Information
AI Technical Summary
Problems solved by technology
Method used
Image
Examples
Embodiment Construction
[0013] Before the present invention is described in detail, it should be noted that in the following description, similar elements are denoted by the same numbers.
[0014] Such as figure 1 , figure 2 As shown, a first preferred embodiment of the fireproof, soundproof and shockproof board 1 of the present invention includes a wood wool layer 10 and a cement layer 20.
[0015] The wood wool layer 10 is formed by mixing most wood wool 11 with calcium chloride, fire retardant and a small amount of cement.
[0016] The inner side of the cement layer 20 is combined with a side of the wood wool layer 10, and the cement layer 20 is made of cement mixed resin and laid with a net 21. The arrangement of the net 21 can strengthen the structure and make cement difficult. In this embodiment, the net 21 is woven with natural fibers, and the natural fibers are oily silk (or coconut silk). In this way, it can meet the environmental protection purpose.
[0017] As shown in Figure 3, when the wal...
PUM
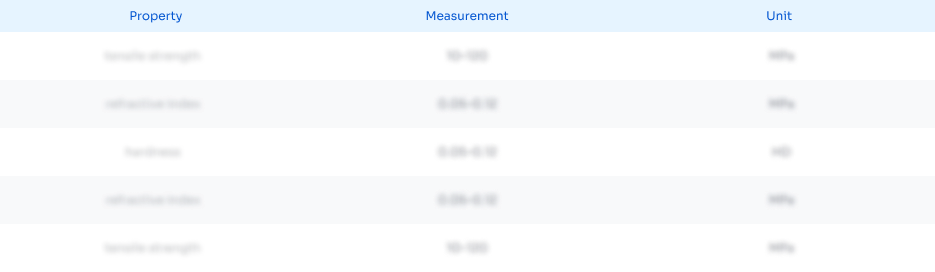
Abstract
Description
Claims
Application Information

- R&D
- Intellectual Property
- Life Sciences
- Materials
- Tech Scout
- Unparalleled Data Quality
- Higher Quality Content
- 60% Fewer Hallucinations
Browse by: Latest US Patents, China's latest patents, Technical Efficacy Thesaurus, Application Domain, Technology Topic, Popular Technical Reports.
© 2025 PatSnap. All rights reserved.Legal|Privacy policy|Modern Slavery Act Transparency Statement|Sitemap|About US| Contact US: help@patsnap.com