Sea water pollution resisting oxide anode and its prepn
An oxide and seawater-resistant technology, applied in the field of electrochemistry, can solve the problems of complex seawater composition, electrocatalytic deactivation, high oxygen content, save material loss and human resources, good oxygen corrosion resistance, and low precious metal content. Effect
- Summary
- Abstract
- Description
- Claims
- Application Information
AI Technical Summary
Problems solved by technology
Method used
Image
Examples
Embodiment 1
[0019] The pretreated titanium matrix is made into a 30mm × 60mm sheet sample, then weigh 1.00 grams of chloroiridic acid, 1.58 grams of ruthenium chloride, measure 25.52 milliliters of dibutyltin dilaurate, and dissolve it in 70 ml of n-butanol Stir evenly in the middle, as an oxide anode coating solution, at this time Ru:Ir:Sn=10:6:84 (wt.%). Brush the prepared coating solution evenly on the surface of the titanium substrate, dry at 60°C for 10 minutes, and then sinter at 470°C for 10 minutes. Repeat the above process until the loading reaches 10g / m 2 , and finally sintered at 470 ° C for 1 h to make an oxide anode. The oxide anode prepared according to the above method has an initial current efficiency of 92%, and after 720 hours of continuous electrolysis in Qingdao seashore natural seawater, the chlorine evolution current efficiency is 77.2%, while adding 20ppm Mn 2+ The current efficiency of chlorine evolution is 74.7% after continuous electrolysis in natural seawate...
Embodiment 2
[0021] Make the pretreated titanium matrix into a 30mm×60mm sheet sample, then weigh 1.00g of chloroiridic acid, 0.85g of ruthenium chloride, measure 0.20ml of dibutyltin dilaurate, and dissolve it in 10ml of n-butanol Stir evenly in the middle, as an oxide anode coating solution, at this time Ru:Ir:Sn=45:50:5 (wt.%). Brush the prepared coating solution evenly on the surface of the titanium substrate, dry at 80°C for 10 minutes, and then sinter at 420°C for 10 minutes. Repeat the above process until the loading reaches 10g / m 2 , and finally sintered at 420 ° C for 1 h to make an oxide anode. The initial current efficiency of the oxide anode prepared according to the above method is 97%, and the chlorine evolution current efficiency is 70.2% after continuous electrolysis in the natural seawater of Qingdao seashore for 720 hours, while adding 20ppm Mn 2+ After 10 days of continuous electrolysis in natural seawater, the current efficiency of chlorine evolution is 68.5%.
Embodiment 3
[0023] The pretreated titanium matrix is made into a 30mm × 60mm sheet sample, then weigh 1.00 grams of chloroiridic acid, 0.79 grams of ruthenium chloride, measure 3.05 milliliters of dibutyltin dilaurate, and dissolve it in 20 ml of n-butanol Stir evenly in the middle, as an oxide anode coating solution, at this time Ru:Ir:Sn=25:30:45 (wt.%). Brush the prepared coating solution evenly on the surface of the titanium substrate, dry at 100°C for 10 minutes, and then sinter at 400°C for 10 minutes. Repeat the above process until the loading reaches 10g / m 2 , and finally sintered at 400 ° C for 1 h to make an oxide anode. The initial current efficiency of the oxide anode prepared according to the above method is 97%, and the chlorine evolution current efficiency is 75.8% after 720 hours of continuous electrolysis in Qingdao coastal natural seawater, while adding 20ppm Mn 2+The current efficiency of chlorine evolution is 76.5% after continuous electrolysis in natural seawater ...
PUM
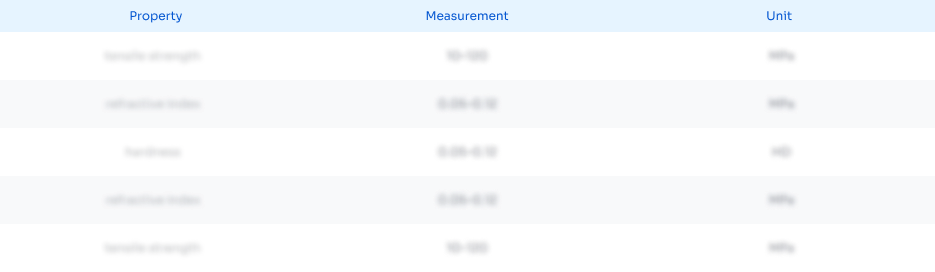
Abstract
Description
Claims
Application Information

- Generate Ideas
- Intellectual Property
- Life Sciences
- Materials
- Tech Scout
- Unparalleled Data Quality
- Higher Quality Content
- 60% Fewer Hallucinations
Browse by: Latest US Patents, China's latest patents, Technical Efficacy Thesaurus, Application Domain, Technology Topic, Popular Technical Reports.
© 2025 PatSnap. All rights reserved.Legal|Privacy policy|Modern Slavery Act Transparency Statement|Sitemap|About US| Contact US: help@patsnap.com