Method for consecutive blanching flax paper pulp in high whiteness through multiple stage
A high-brightness, pulp technology, applied in the field of pulp bleaching, can solve the problems of high production cost, low whiteness of bleached pulp, large discharge, etc., achieve low environmental pollution load, improve pulp quality, and reduce waste water discharge. Effect
- Summary
- Abstract
- Description
- Claims
- Application Information
AI Technical Summary
Problems solved by technology
Method used
Image
Examples
specific Embodiment approach 1
[0033] Specific embodiment one: in conjunction with Fig. 1, the flax pulp continuous multistage bleaching method of the present embodiment comprises the following steps:
[0034] 1. Cooking, washing and grinding
[0035] After the flax raw material is cooked by the alkaline sulfite method, the cooked slurry is fully washed and cut by the washing machine, and the impurities are removed by screening and purification equipment, and the slurry after the removal of impurities is adjusted to be suitable for storage The concentration is put into the semi-slurry buffer tank.
[0036] 2. Chlorination (C)
[0037] After washing, grinding, screening, and purification, the pulp and chlorine gas are fully mixed and then enter the chlorination tower. The chlorine gas reacts with the residual lignin in the pulp, and the lignin degrades into fragments soluble in water or dilute lye. The viscosity of the pulp is reduced, and the carbohydrates are degraded to a certain extent. Only a part of ...
specific Embodiment approach 2
[0042] Specific embodiment two: put 3000 kg of absolute dry flax raw materials, sulfite, sodium hydroxide and a certain proportion of water into the digester, and cook at a temperature of 168-170°C for a certain period of time to obtain unbleached flax pulp. After washing, grinding, screening and purification, after four stages of continuous bleaching including chlorination (C), alkali treatment (E), pretreatment (S) and hydrogen peroxide (P), high whiteness flax pulp (whiteness 85% ISO or above), the specific conditions are as follows:
[0043] 1. Cooking conditions (Table 1):
[0044] Nabeji
1
2
3
4
Pot loading time (h)
2.0
2.0
2.0
2.0
quality
Condition
Bone content (%)
4.6
4.6
4.6
4.6
Short fiber content (%)
14.3
14.3
14.3
14.3
Average pile length (mm)
53
53
53
53
Alkali ratio (%) ...
specific Embodiment approach 3
[0081] Specific embodiment three: the difference between this embodiment and specific embodiment two is that the specific process conditions are as follows:
[0082] 1. Cooking process conditions:
[0083] Pot capacity: 3200±100kg;
[0084] Sodium hydroxide: 4.0%, dosage: 128kg;
[0085] Anthraquinone derivatives: 0.05%, dosage: 1.6kg;
[0086] Liquid ratio: 1:2.6, additional water: 7.8T;
[0087] Liquid temperature: 75~80℃
[0088] Cooking curve:
[0089] Dry run: 90 minutes
[0090] One heating: 60 minutes 0~0.45Mpa
[0091] Small steam release: 0.45~0Mpa in 10 minutes
[0092] Second heating: 30 minutes 0~0.65Mpa
[0093] Heat preservation: 2.5 hours 0.65~0.75Mpa
[0094] Hardness: ≤6 (Kappa value), residual alkali: only check but not control;
[0095] 2. Bleaching conditions:
[0096] (1) Section C:
[0097] Chlorine consumption: 1.0% (for absolute dry pulp);
[0098] Slurry concentration: 2.0%~3.0%;
[0099] Time: 30-40 minutes;
[0100] Temperature: room t...
PUM
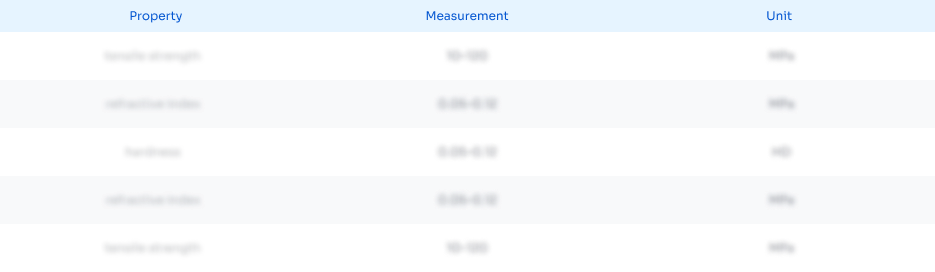
Abstract
Description
Claims
Application Information

- R&D
- Intellectual Property
- Life Sciences
- Materials
- Tech Scout
- Unparalleled Data Quality
- Higher Quality Content
- 60% Fewer Hallucinations
Browse by: Latest US Patents, China's latest patents, Technical Efficacy Thesaurus, Application Domain, Technology Topic, Popular Technical Reports.
© 2025 PatSnap. All rights reserved.Legal|Privacy policy|Modern Slavery Act Transparency Statement|Sitemap|About US| Contact US: help@patsnap.com