Method for fabricating quartz base plate of optical device
A technology of quartz substrate and manufacturing method, which is applied in the direction of manufacturing tools, glass manufacturing equipment, glass molding, etc., can solve the problems of damage to workers' skin and respiratory tract, difficult precision of quartz substrate, low production speed and other problems, and achieve labor-saving economy Efficiency and ease of operation, elimination of local surface hidden cracks, and elimination of jig positioning errors
- Summary
- Abstract
- Description
- Claims
- Application Information
AI Technical Summary
Problems solved by technology
Method used
Image
Examples
Embodiment Construction
[0032] figure 1 It is a three-dimensional schematic diagram of a quartz substrate processed by general machinery, 1 is the optical fiber positioning groove, and 2 is the quartz rod. This kind of quartz substrate has undergone a series of processes such as material selection, jig positioning, waxing and fixing, grinding and cutting, and wax melting. The quartz substrate produced by the engineering operation, due to the size error of the material, the positioning error of the fixture, the movement error of the quartz rod when pouring wax, the error of the machine tool, the error of grinding and cutting, the wear error of the diamond grinding wheel and other factors, the accuracy of the produced quartz substrate is It is not easy to control, and the optical fiber positioning groove of the quartz substrate is deformed and offset. Therefore, this manufacturing method has poor production stability, low product quality, and low pass rate.
[0033] Fig. 2 is a three-dimensional schema...
PUM
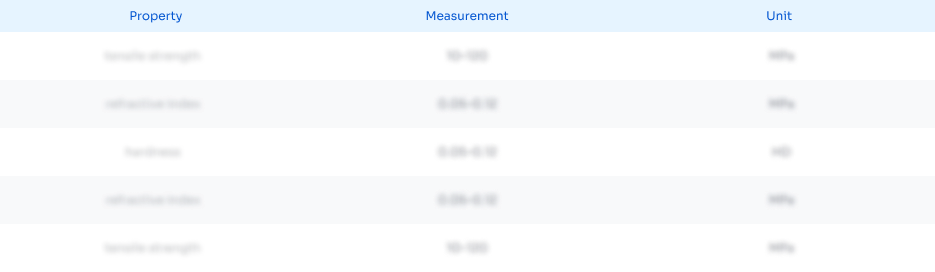
Abstract
Description
Claims
Application Information

- R&D Engineer
- R&D Manager
- IP Professional
- Industry Leading Data Capabilities
- Powerful AI technology
- Patent DNA Extraction
Browse by: Latest US Patents, China's latest patents, Technical Efficacy Thesaurus, Application Domain, Technology Topic, Popular Technical Reports.
© 2024 PatSnap. All rights reserved.Legal|Privacy policy|Modern Slavery Act Transparency Statement|Sitemap|About US| Contact US: help@patsnap.com