Cellulose/montmorillonite nanometer composite material and its preparation method
A nano-composite material and montmorillonite technology, which is applied in the chemical industry, can solve the problems of environmental pollution, low utilization rate of straw, waste of natural resources, etc., achieve wide application prospects, facilitate industrial production, and inhibit thermal decomposition.
- Summary
- Abstract
- Description
- Claims
- Application Information
AI Technical Summary
Problems solved by technology
Method used
Image
Examples
Embodiment 1
[0029] Embodiment 1, the preparation of cellulose / montmorillonite nanocomposite material:
[0030] ①Preparation of straw cellulose: crush corn stalks, add 120 times the mass of straw powder and 60% nitric acid solution, reflux at 120°C for 2 hours; then add an equimolar amount of nitric acid to reflux 1h, suction filtration, washing with distilled water, drying to obtain straw cellulose;
[0031] ②Modification of montmorillonite: put natural montmorillonite in water, stir and heat in a constant temperature water bath at 40°C for 30-60 minutes, then let it stand to form a montmorillonite aqueous dispersion; take 0.5 times the mass of natural montmorillonite Dodecyltrimethylammonium bromide is placed in water, and hydrochloric acid of 1 times the mass of natural montmorillonite is added to adjust to form a protonated solution, and the protonated solution is added dropwise to the montmorillonite water dispersion, and ultrasonically vibrated After 3 to 4 hours, filter with suctio...
Embodiment 2
[0033] Embodiment 2, the preparation of cellulose / montmorillonite nanocomposite material:
[0034] ①Preparation of straw cellulose: crush the wheat straw, add it into a nitric acid solution with 90 times the weight of the straw powder and a concentration of 62%, and reflux at 110° C. for 3 hours; then add an equimolar amount of nitric acid to reflux 1.5h, suction filtration, washing with distilled water, drying to obtain straw cellulose;
[0035] ②Modification of montmorillonite: put natural montmorillonite in water, stir and heat in a constant temperature water bath at 50°C for 30-60 minutes, then let it stand to form a montmorillonite aqueous dispersion; take 0.3 times the mass of natural montmorillonite Cetyltrimethylammonium bromide is placed in water, and hydrochloric acid of 0.8 times the quality of natural montmorillonite is added to adjust to form a protonated solution, and the protonated solution is added dropwise to the montmorillonite aqueous dispersion, and ultraso...
Embodiment 3
[0037] Embodiment 3, the preparation of cellulose / montmorillonite nanocomposite material:
[0038] ①Preparation of straw cellulose: crush corn stalks, add them to a nitric acid solution with a concentration of 65% and 60 times the weight of the straw powder, and reflux at 100°C for 2.5 hours; Reflux for 1.3h, suction filter, wash with distilled water, and dry to obtain straw cellulose;
[0039] ②Modification of montmorillonite: put the natural montmorillonite in water, stir and heat it in a constant temperature water bath at 60°C for 30-60 minutes, and then let it stand to form an aqueous dispersion of montmorillonite; take 0.4 times the mass of natural montmorillonite Octadecyltrimethylammonium chloride is placed in water, and hydrochloric acid of 1 times the mass of natural montmorillonite is added to adjust to form a protonated solution, and the protonated solution is added dropwise to the montmorillonite aqueous dispersion, and ultrasonically vibrated After 3 to 4 hours, ...
PUM
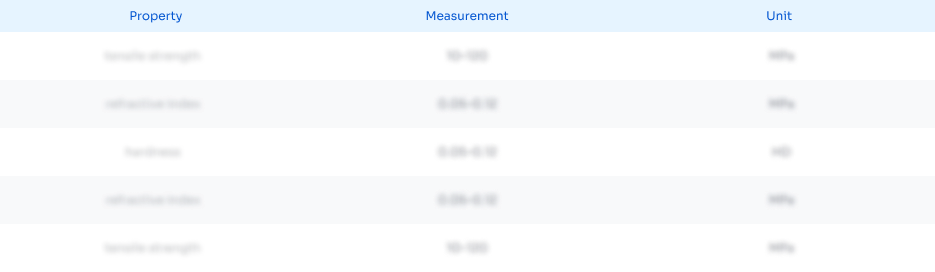
Abstract
Description
Claims
Application Information

- R&D Engineer
- R&D Manager
- IP Professional
- Industry Leading Data Capabilities
- Powerful AI technology
- Patent DNA Extraction
Browse by: Latest US Patents, China's latest patents, Technical Efficacy Thesaurus, Application Domain, Technology Topic, Popular Technical Reports.
© 2024 PatSnap. All rights reserved.Legal|Privacy policy|Modern Slavery Act Transparency Statement|Sitemap|About US| Contact US: help@patsnap.com