Combined process for organic solvent extracting zinc and wet zinc refining
A technology of zinc hydrometallurgy and organic solvents, applied in the combined process field, can solve the problems of raw material shortage, low grade, and insufficient production capacity, etc., and achieve the effect of flexible configuration
- Summary
- Abstract
- Description
- Claims
- Application Information
AI Technical Summary
Problems solved by technology
Method used
Image
Examples
example 1
[0025] the element
[0026] After leaching with dilute sulfuric acid, the solution contains 52 g / L of Zn, 60 mg / L of Co, and 128 mg / L of Ni. It is very difficult to remove Co and Ni by the solution purification technology in the conventional hydrometallurgy process.
[0027] the element
[0028] After separating Zn from Co and Ni through this process, zinc ions are selectively transferred to the waste electrolyte, and then electrolytically produced through the leaching and purification process of the conventional wet zinc smelting process. The raffinate is returned to the acid leaching of low-grade and high-impurity zinc materials and recycled, achieving the purpose of using high Co and Ni zinc oxide ore with conventional hydrometallurgy zinc production capacity, and no waste water is produced. The organic matter after stripping is also returned to the leaching of low-grade and high-impurity zinc materials for recycling.
example 2
[0031] Fe in solution is Fe +2 , due to Fe and SO 4 2- The content is high, it is not suitable for the production of zinc chloride products, the use of P 204 After the zinc is extracted, the electrolytic waste liquid is used for back extraction, and the zinc ions can be transferred to the waste electrolyte.
[0032] Dilute the solution to 60 g / L Zn with 20% P 204 Solvent extraction mixed with 260# kerosene, the extraction ratio is O / A=2.5 / 1, the acid produced is neutralized with NaOH solution during the extraction process, after a first-stage extraction, the extraction mixing time is 5 minutes, and the extraction temperature is 20 ° C ~ 40 °C, the end point pH is 3.6, and the raffinate contains less than 0.5 g / L of zinc. After phase separation and clarification, use H 2 SO 4 180 g / L of waste electrolyte is used for back-extracting zinc, the stripping ratio is O / A=2 / 1, the stripping temperature is 20°C-40°C, and the zinc content of the waste liquid increases from 4...
example 3
[0034] A zinc-containing mineral contains 8.54% zinc, of which the oxidation rate of zinc is 84.5%.
[0035] Leach with a solution containing dilute sulfuric acid, the solution contains 10.2 g / l to 12.5 g / l of zinc, 0.7 mg / l to 1.5 mg / l of Fe, and the zinc leaching rate is 72% to 75%.
[0036] with 35%P 204 It is mixed with 260# kerosene to form an extraction solvent, and it is subjected to three-stage countercurrent extraction, O / A=1 / 1, the extraction mixing time is 1 minute, the extraction temperature is 30°C, the raffinate contains Zn 2.5-4.5 g / L, and contains H 2 SO 4 13-15 g / L, and the organic phase contains Zn 8-10 g / L. The organic phase is back-extracted with a waste electrolyte containing 180 g / L of acid and 45 g / L of Zn. The back-extraction ratio is O / A=5 / 1, the back-extraction temperature is 40°C, and the back-extraction solution contains 95-100 g / L of Zn. Liters with H 2 SO 4 95-100 g / L, the back-extraction solution is returned to conventional wet zinc leaching...
PUM
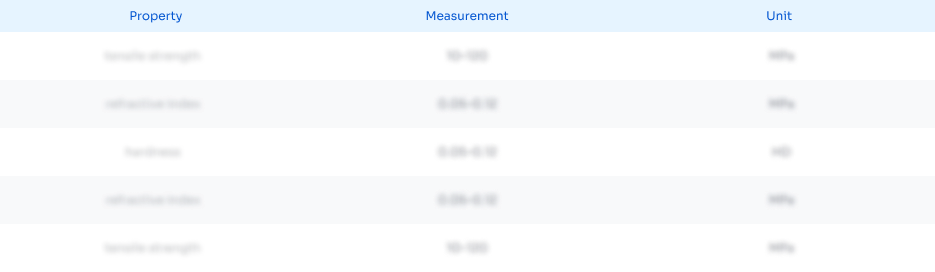
Abstract
Description
Claims
Application Information

- R&D Engineer
- R&D Manager
- IP Professional
- Industry Leading Data Capabilities
- Powerful AI technology
- Patent DNA Extraction
Browse by: Latest US Patents, China's latest patents, Technical Efficacy Thesaurus, Application Domain, Technology Topic, Popular Technical Reports.
© 2024 PatSnap. All rights reserved.Legal|Privacy policy|Modern Slavery Act Transparency Statement|Sitemap|About US| Contact US: help@patsnap.com