Foam nickel, and method for fabricating the foam nickel, and battery of using the foam nickel
A production method and foamed nickel technology are applied in the field of foamed nickel batteries, which can solve the problems of poor current collection effect of battery electrode substrates, low utilization rate of electrode active materials, insufficient roughness of foamed nickel, etc., and achieve low internal resistance and low production. Cost, high capacity effect
- Summary
- Abstract
- Description
- Claims
- Application Information
AI Technical Summary
Problems solved by technology
Method used
Image
Examples
Embodiment 1
[0028] Production of nickel foam:
[0029] Take two rolls of continuous polyurethane sponge (aperture 110PPI, thickness 1.9mm, width 1000mm), each 50m for conduction, respectively marked as I, II, conduction is coated with conductive adhesive process, I, II under the same process conditions Coating conductive adhesive, the process of coating conductive adhesive is polyurethane sponge-dipping glue-squeezing glue-drying (at 70-120°C), the solid content of the glue is 7-10%, the pH value is 10-11, and the temperature is 10-30℃, viscosity 5-20mPa.s.
[0030] Put I and II into the ordinary nickel foam electrodeposition bath, and electrodeposit them under the same process conditions. The process conditions are as follows, I deposit 430g / m 2 Electrodeposition is terminated after nickel, I is the finished product of ordinary nickel foam electroplating; II deposits 230g / m 2 Nickel is put into the electro-deposition tank liquid that adds copper powder of the present invention to cont...
Embodiment 2
[0062] Change the content of copper powder into 20g / L, all the other are with the method for embodiment 1, make common nickel foam I, the foam nickel II that roughening strengthens current collection effect; Adopt these two kinds of foam nickel respectively according to the method in embodiment 1 Battery manufacturing method is made into each 30 of SC-1900mAh nickel-cadmium batteries, and the battery that common foam nickel I makes is marked as A1 group, and the battery that foam nickel II of the present invention makes is marked as B1 group.
[0063] Performance Test Comparison 2.1
[0064] The physical and chemical properties of the nickel foam II with the above-mentioned roughening and enhanced current collection effect and ordinary nickel foam I were used for physical and chemical performance tests. The results are shown in Table 2.1:
[0065] performance
[0066] It can be seen from the above table that, except for the difference in copper and nickel content, th...
Embodiment 3
[0072] Except that the content of the copper powder was changed to 5g / L, the rest were the same as in Example 1, and ordinary nickel foam I and nickel foam II with roughening enhanced current collection effect were obtained. Adopt these two kinds of nickel foams to make respectively 30 SC-1900mAh nickel-cadmium batteries according to the battery manufacturing method in embodiment 1, the battery that common nickel foam I makes is marked as A2 group, the battery that nickel foam II of the present invention makes is marked as Group B2.
[0073] Performance Test Comparison 3.1
[0074] The physical and chemical properties of nickel foam II and ordinary nickel foam I with the above-mentioned roughening and enhanced current collection effect were used for physical and chemical performance tests, and the results are shown in Table 3.1:
[0075] performance
[0076] It can be seen from the above table that, except for the difference in copper and nickel content, the foamed ...
PUM
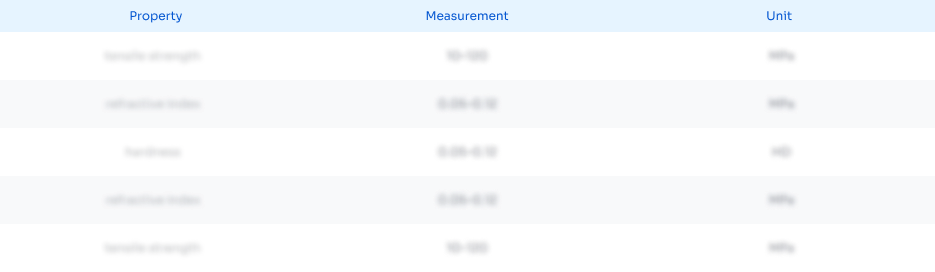
Abstract
Description
Claims
Application Information

- R&D
- Intellectual Property
- Life Sciences
- Materials
- Tech Scout
- Unparalleled Data Quality
- Higher Quality Content
- 60% Fewer Hallucinations
Browse by: Latest US Patents, China's latest patents, Technical Efficacy Thesaurus, Application Domain, Technology Topic, Popular Technical Reports.
© 2025 PatSnap. All rights reserved.Legal|Privacy policy|Modern Slavery Act Transparency Statement|Sitemap|About US| Contact US: help@patsnap.com