Diene silicoxyane linking disbenzocyclobutylene monomer and process for preparing prepolymer
A technology of dienyl siloxane bridge and benzocyclobutene, applied in the field of preparation of dienyl siloxane bridged bisbenzocyclobutene monomer and prepolymer, can solve the molecular weight of prepolymer Wide distribution, non-recyclable solvent, long polymerization time and other problems, to achieve the effect of shortening the production cycle, shortening the polymerization time, and reducing energy consumption
- Summary
- Abstract
- Description
- Claims
- Application Information
AI Technical Summary
Problems solved by technology
Method used
Image
Examples
Embodiment 1
[0045] In a 50ml two-neck flask equipped with a magnetic stirring bar, first add 32mmol NaOAc 2.624g, distilled water 5.8ml and stir to dissolve, then add [C 2 Py]PF 6 2.9g, Pd(OAc) 2 4mg, 8mmol DVS 1.488g, 16mmol4-BrBCB 2.912g, then pass nitrogen gas to remove the air in the reaction flask, and react at 90°C for 22 hours under nitrogen atmosphere; extract the reaction solution with petroleum ether (3×20ml), and combine Organic phase, anhydrous Na 2 SO 4 After drying, the organic phase was filtered on silica gel, rinsed with petroleum ether, and the eluent was concentrated to dryness under reduced pressure to obtain 2.5 g of a colorless or light yellow oily liquid, with a yield of 80%. 1 HNMR (400MHz, CDCl 3 ), 6.89-7.25 (br, 6H), 6.31-6.37 (d, 4H), 3.16 (s, 8H), 0.23 (s, 12H). The ionic liquid was washed and dried to obtain a white solid [C 2 Py]PF 6 2.8g.
Embodiment 2
[0047] In the 50ml two-neck flask equipped with a magnetic stirrer, first add 32mmol NaOAc 2.624g, distilled water 5.8ml and stir to dissolve, then add the recovered [C 2 Py]PF 6 2.9g, Pd(OAc) 2 4mg, 8mmol DVS1.488g, 16mmol 4-BrBCB 2.912g, then pass nitrogen gas to remove the air in the reaction flask, and react at 90°C for 22 hours under nitrogen atmosphere; the reaction solution was extracted with petroleum ether (3×20ml), Combined organic phases, anhydrous Na 2 SO 4 After drying, the organic phase was filtered through silica gel, rinsed with petroleum ether, and the eluent was concentrated to dryness under reduced pressure to obtain 2.47 g of a colorless or light yellow oily liquid with a yield of 79%. The ionic liquid was washed and dried to obtain a white solid [C 2 Py]PF 6 2.78g.
Embodiment 3
[0049] In the 50ml two-neck flask equipped with a magnetic stirrer, first add 32mmol NaOAc 2.624g, distilled water 5.8ml and stir to dissolve, then add the recovered [C 2 Py]PF 6 2.9g, Pd(OAc) 2 4mg, 8mmol DVS1.488g, 16mmol 4-BrBCB 2.912g, then pass nitrogen gas to remove the air in the reaction flask, and react at 90°C for 22 hours under nitrogen atmosphere; the reaction solution was extracted with petroleum ether (3×20ml), Combined organic phases, anhydrous Na 2 SO 4 After drying, the organic phase was filtered through silica gel, rinsed with petroleum ether, and the eluent was concentrated to dryness under reduced pressure to obtain 2.55 g of a colorless or light yellow oily liquid, with a yield of 81.7%. The ionic liquid was washed and dried to obtain a white solid [C 2 Py]PF 6 2.8g.
PUM
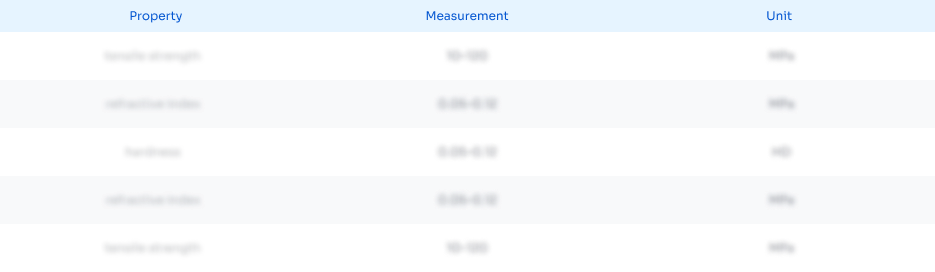
Abstract
Description
Claims
Application Information

- R&D
- Intellectual Property
- Life Sciences
- Materials
- Tech Scout
- Unparalleled Data Quality
- Higher Quality Content
- 60% Fewer Hallucinations
Browse by: Latest US Patents, China's latest patents, Technical Efficacy Thesaurus, Application Domain, Technology Topic, Popular Technical Reports.
© 2025 PatSnap. All rights reserved.Legal|Privacy policy|Modern Slavery Act Transparency Statement|Sitemap|About US| Contact US: help@patsnap.com