Superplasticiser for cement granule dispersion and its synthesis method
A technology of superplasticizers and granules, which is applied in the field of dispersants for cement granules, and can solve the problems of easy environmental pollution, long reaction time, and high energy consumption.
- Summary
- Abstract
- Description
- Claims
- Application Information
AI Technical Summary
Problems solved by technology
Method used
Image
Examples
preparation example Construction
[0026] The monomer a used in the preparation of the copolymer of the present invention will be described below, wherein EO stands for ethylene oxide and PO stands for propylene oxide.
[0027] AE-1: Monoallyl ether of EO adduct (average molecular weight of added EO is 950)
[0028] AE-2: Monoallyl ether of adduct of EO (average molecular weight of added EO is 1200)
[0029] AE-3: Monoallyl ether of EO and PO block adduct (the average molecular weight of added EO is 400, and the average molecular weight of PO is 1500)
[0030] AE-4: Monoallyl ether of EO and PO block adducts (the average molecular weight of added EO is 750, and the average molecular weight of PO is 750)
[0031] AE-5: Monoallyl alcohol ether of adduct of EO (average molecular weight of added EO is 2288)
[0032] AE-6: Monoallyl alcohol ether of the adduct of methanol and EO (the average molecular weight of the added EO is 2288)
[0033] AE-7: Monoallyl alcohol ether of EO and PO block adduct (the average molecular ...
Embodiment 1
[0036] Add 81.5 parts of AE-1 into a 500ml four-necked flask equipped with a stirrer, thermometer and dripping device, while adding 75 parts of deionized water. After stirring and dissolving, add 0.008 parts of ferrous sulfate heptahydrate and 1.5 parts of 30% Of hydrogen peroxide. At 30℃, simultaneously add maleic anhydride solution (8.9 parts of maleic anhydride dissolved in 45 parts of deionized water, after stirring to dissolve, add 0.018 parts of ferrous sulfate heptahydrate and 3.125 parts of 30% hydrogen peroxide) and formaldehyde Sodium sulfite solution (1.81 parts of sodium formaldehyde hyposulfite dissolved in 10 grams of deionized water), the dripping time is controlled at 70 minutes, and the reaction temperature is not higher than 38°C. After the dripping is completed, keep it at 35°C for 30 min, and neutralize it with 25% NaOH to a pH of 6.22.
Embodiment 2
[0038] Add 81.5 parts of AE-2 into a 500ml four-necked flask equipped with a stirrer, thermometer and dripping device, while adding 75 parts of deionized water. After stirring and dissolving, add 0.008 parts of ferrous sulfate heptahydrate and 1.5 parts of 30% Of hydrogen peroxide. At 30℃, simultaneously add maleic anhydride solution (8.9 parts of maleic anhydride dissolved in 45 parts of deionized water, after stirring to dissolve, add 0.018 parts of ferrous sulfate heptahydrate and 3.125 parts of 30% hydrogen peroxide) and formaldehyde Sodium sulfite solution (1.81 parts of sodium formaldehyde hyposulfite dissolved in 10 grams of deionized water), the dripping time is controlled at 70 minutes, and the reaction temperature is not higher than 38°C. After the dripping is completed, keep it at 35°C for 30 min, and neutralize it with 25% NaOH to a pH of 6.22.
PUM
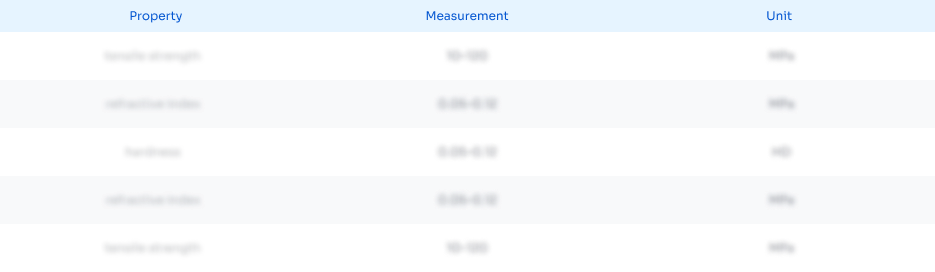
Abstract
Description
Claims
Application Information

- R&D
- Intellectual Property
- Life Sciences
- Materials
- Tech Scout
- Unparalleled Data Quality
- Higher Quality Content
- 60% Fewer Hallucinations
Browse by: Latest US Patents, China's latest patents, Technical Efficacy Thesaurus, Application Domain, Technology Topic, Popular Technical Reports.
© 2025 PatSnap. All rights reserved.Legal|Privacy policy|Modern Slavery Act Transparency Statement|Sitemap|About US| Contact US: help@patsnap.com