Production method of zinc indium by pressurized acid leaching neutralization precipitation separation indium from indium containing high iron zinc sulfide concentrate
A zinc sulfide concentrate, precipitation separation technology, applied in the direction of improving process efficiency, can solve the problems of reducing the volume of indium solution extracted, and achieve the effects of efficient direct leaching, process enhancement, and reduced processing capacity
- Summary
- Abstract
- Description
- Claims
- Application Information
AI Technical Summary
Problems solved by technology
Method used
Image
Examples
Embodiment 1
[0008] Example 1. Indium-containing high-iron zinc sulfide concentrate contains 10% iron, 0.025% indium, and 38.0% zinc. The concentrate is finely ground, and 98% passes through a 0.043mm sieve.
[0009] Slurry the finely ground indium-containing high-iron zinc sulfide concentrate and zinc electrowinning waste liquid, put it into an acid-resistant autoclave made of titanium with a volume of 4L, and carry out a period of continuous oxygen flow at a temperature of 140°C and a pressure of 1.0MPa leach.
[0010] The zinc leaching rate is 99.28%, the indium leaching rate is 94.43%, and the sulfur conversion rate is 78.38%. The leaching solution contains 114.0g / L of zinc and 42.92mg / L of indium. The leaching slag contains 0.67% zinc and 53.88% elemental sulfur.
[0011] Add zinc sulfide concentrate to the leaching solution and reduce at 85°C for 90 minutes, then add limestone powder to neutralize, the indium precipitation rate is 95.68%, and the indium precipitation residue In0.214...
Embodiment 2
[0013] Example 2. The indium-containing high-iron zinc sulfide concentrate has an iron content of 18%, an indium content of 0.042%, and a zinc content of 40%. The concentrate is finely ground, and 99.0% passes through a 0.043mm sieve.
[0014] Slurry the finely ground indium-containing high-iron zinc sulfide concentrate and zinc electrowinning waste liquid, put it into a 4L titanium autoclave, and carry out one-stage continuous oxygen leaching at a temperature of 150°C and a pressure of 1.4MPa.
[0015] The zinc leaching rate is 99.79%, the indium leaching rate is 98.02%, and the sulfur conversion rate is 81.98%. The leaching solution contains 132g / L of zinc and 62.44mg / L of indium. The leaching slag contains 0.87% zinc and 55.23% elemental sulfur.
[0016] Add zinc sulfide concentrate to the leaching solution and reduce at 90°C for 90 minutes, then add limestone powder to neutralize, the indium precipitation rate is 98.76%, and the indium precipitation residue In0.617% is obt...
Embodiment 3
[0018] Example 3, the indium-containing high-iron zinc sulfide concentrate contains 25% iron, 0.09% indium, and 48% zinc. The concentrate is finely ground, and 98.5% passes through a 0.043mm sieve.
[0019] Slurry the finely ground indium-containing high-iron zinc sulfide concentrate and zinc electrowinning waste liquid into an acid-resistant autoclave made of titanium with a volume of 4L, and carry out two-stage continuous passage at a temperature of 160°C and a pressure of 1.6MPa. Oxygen leaching.
[0020] The zinc leaching rate is 99.48%, the indium leaching rate is 98.21%, and the sulfur conversion rate is 79.62%. The leaching solution contains 141g / L of zinc and 55.63mg / L of indium. The leaching slag contains 1.02% zinc and 52.42% elemental sulfur.
[0021] Add zinc sulfide concentrate to the leaching solution and reduce at 95°C for 90 minutes, then add limestone powder to neutralize, the indium precipitation rate is 97.91%, and the indium precipitation residue In0.511% ...
PUM
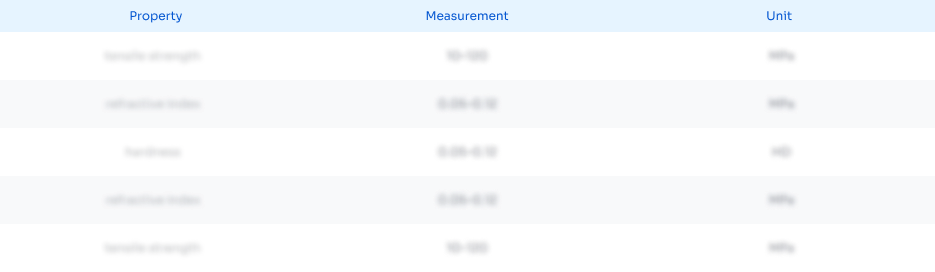
Abstract
Description
Claims
Application Information

- R&D
- Intellectual Property
- Life Sciences
- Materials
- Tech Scout
- Unparalleled Data Quality
- Higher Quality Content
- 60% Fewer Hallucinations
Browse by: Latest US Patents, China's latest patents, Technical Efficacy Thesaurus, Application Domain, Technology Topic, Popular Technical Reports.
© 2025 PatSnap. All rights reserved.Legal|Privacy policy|Modern Slavery Act Transparency Statement|Sitemap|About US| Contact US: help@patsnap.com