Predecomposition kiln by pass air relief and coal gangue dewatering technology
A technology of precalcining kiln and bypass ventilation, which is applied in the field of coal gangue dehydration process, and can solve the problems of clinker and cement quality decline, alkali-aggregate reaction, and deterioration of calcination conditions, etc.
- Summary
- Abstract
- Description
- Claims
- Application Information
AI Technical Summary
Problems solved by technology
Method used
Image
Examples
Embodiment 1
[0016] Example 1, such as figure 1 , the exhaust gas discharged from the primary cyclone separator 2 directly enters the quenching chamber, sprays water and mixes with cold air, and directly enters the electrostatic precipitator after lowering the temperature. The waste gas from the secondary and tertiary cyclone separators 3 and 4, that is, the coal gangue powder cooling system, has a temperature of about 150° C. and can be directly used for coal gangue grinding and drying.
Embodiment 2
[0017] Embodiment 2: as figure 2 , the waste gas discharged from the primary cyclone separator 2 is introduced into the humidification tower 7 for humidification, and after being collected by the electrostatic precipitator 8, it is discharged by the smoke exhaust fan 9 and the chimney 10.
Embodiment 3
[0018] Embodiment 3: as figure 2 , the exhaust gas discharged from the first-stage cyclone separator 2 directly enters the 14th to 15th-stage cyclone connecting pipe of the decomposition kiln, and then enters the preheater system of the precalciner kiln.
[0019] The present invention can also be used for precalcining the hot gas of the grate cooler of the kiln, and other hot gases can also be used.
PUM
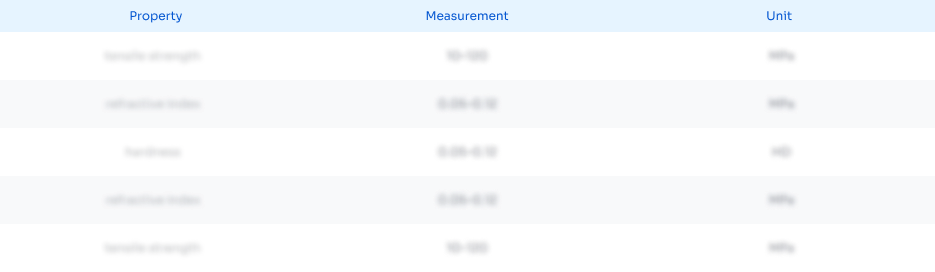
Abstract
Description
Claims
Application Information

- R&D
- Intellectual Property
- Life Sciences
- Materials
- Tech Scout
- Unparalleled Data Quality
- Higher Quality Content
- 60% Fewer Hallucinations
Browse by: Latest US Patents, China's latest patents, Technical Efficacy Thesaurus, Application Domain, Technology Topic, Popular Technical Reports.
© 2025 PatSnap. All rights reserved.Legal|Privacy policy|Modern Slavery Act Transparency Statement|Sitemap|About US| Contact US: help@patsnap.com