Spring surface acoustic wave device manufacturing method, spring surface acoustic wave device
A technology of surface acoustic wave and a manufacturing method, which is applied in the manufacture of surface acoustic wave devices and the field of surface acoustic wave devices, can solve problems such as the insulation properties of harmful surface acoustic wave components, achieve good insulation properties, high-function communication devices, prevent thermoelectricity the effect of destruction
- Summary
- Abstract
- Description
- Claims
- Application Information
AI Technical Summary
Problems solved by technology
Method used
Image
Examples
Embodiment 1
[0145] A surface acoustic wave device was manufactured by the method shown in FIG. 1( a ) to FIG. 1( j ).
[0146] The main surface of the piezoelectric substrate 2 (substrate thickness: 250 μm) formed on the lithium tantalate single crystal substrate in the Y-cut X-transport direction at 38.7° is formed into a film of Ti / Al-1 mass% Cu / Ti from the substrate side by sputtering 4-layer electrode layer formed of / Al-1 mass% Cu. The film thicknesses are 6nm / 209nm / 6nm / 209nm, respectively.
[0147] Next, if image 3 As shown, the electrode layer is patterned by photolithography and RIE to form a plurality of surface acoustic wave element regions, which have: filter regions having IDT electrodes 3 , input electrode parts 5 and output electrode parts 6 are formed. In addition, at this time, the ground electrode portion 8 , the connection electrode 4 and the annular electrode 7 are also formed simultaneously.
[0148] As the etching gas at this time, a mixed gas of BC13 and C12 was ...
Embodiment 2
[0166] A duplexer-type surface acoustic wave device having a transmission-side filter region and a reception-side filter region in a piezoelectric substrate was fabricated by the method shown in FIGS. 1( a ) to 1( j ).
Embodiment 2-1
[0168] As in Example 1, four electrode layers were formed on the main surface of the lithium tantalate single crystal substrate.
[0169] Next, the electrode layer is patterned by photolithography and RIE to form a plurality of filter regions, which have the following functions: forming a transmission-side filter region with an IDT electrode 3, an input electrode portion 5, and an output electrode portion 6 and a reception-side filter region; device area. In addition, at this time, the ground electrode portion 11 , the connection electrode 4 , and the annular electrode 7 are also formed at the same time.
[0170] As the etching gas at this time, a mixed gas of BC13 and C12 was used.
[0171] The line width of the comb-shaped electrodes forming the IDT electrodes 3 and the distance between adjacent comb-shaped electrodes are both approximately 1 μm.
[0172] Next, a conductor layer made of pure Al was formed on the other surface of the piezoelectric substrate 2 by a sputterin...
PUM
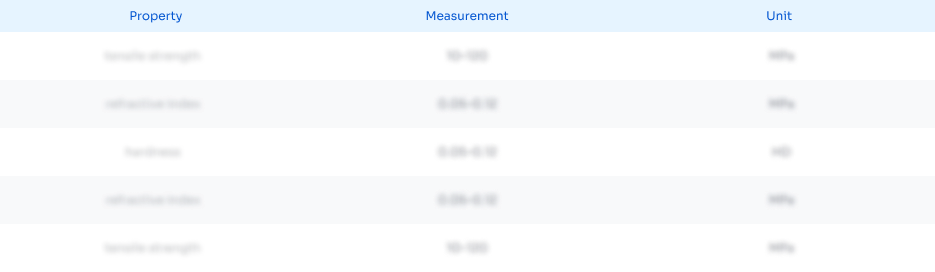
Abstract
Description
Claims
Application Information

- Generate Ideas
- Intellectual Property
- Life Sciences
- Materials
- Tech Scout
- Unparalleled Data Quality
- Higher Quality Content
- 60% Fewer Hallucinations
Browse by: Latest US Patents, China's latest patents, Technical Efficacy Thesaurus, Application Domain, Technology Topic, Popular Technical Reports.
© 2025 PatSnap. All rights reserved.Legal|Privacy policy|Modern Slavery Act Transparency Statement|Sitemap|About US| Contact US: help@patsnap.com