Functional fiber and its manufacturing method
A technology of functional fiber and manufacturing method, which is applied in fiber processing, rayon manufacturing, fiber chemical characteristics, etc., can solve the problem of microcapsule essence falling off, far-infrared health care functional fiber, poor fragrance function stability and durability, etc. problems, to achieve the effect of easy storage, avoid affecting the hand of the fabric, and avoid being intolerant to washing
- Summary
- Abstract
- Description
- Claims
- Application Information
AI Technical Summary
Problems solved by technology
Method used
Examples
Embodiment 1
[0025] Take 97.9 parts of dried polyethylene terephthalate (percentage by weight, the same below), 2 parts of alumina powder, and 0.1 part of γ-glycidoxypropyltrimethoxysilane. After fully mixing, Extruded by twin-screw at 270°C, pelletized. The fiber cortex material is produced; take 84 parts of polyethylene, 4 parts of paraffin, and 12 parts of ethyl vanillin. After thorough mixing, extrude through twin-screw at 150° C., and granulate. The fiber core layer material is produced; after the obtained sheath-core material is fully dried, the winding yarn is spun with a skin-core composite spinning machine according to the weight ratio of the fiber skin to core of 7:3; , stretched 3 times, then relaxed heat-setting, cutting, to obtain the functional fiber. It was determined that the far-infrared emissivity of the obtained fiber was 82% (100° C.).
Embodiment 2
[0027]Take 92.6 parts of polypropylene with a melt index of 50, 4 parts of alumina powder, 3 parts of magnesium oxide powder, and 0.4 part of γ-methacryloxytrimethoxysilane. Twin-screw extrusion, granulation. Manufacture the fiber cortex material; take 87 parts of polypropylene (MI=25), 3 parts of ethylene-vinyl acetate (EVA), and 10 parts of vanillin. grain. Manufacture the fiber core layer material; after fully drying the sheath-core material, according to the sheath-to-core ratio of the fiber is 6:4, the coiled yarn is spun on the skin-core composite spinning machine; then the coiled yarn is heated at 65°C Draw down 4 times, can obtain described functional fiber. It was determined that the far-infrared emissivity of the obtained fiber was 86% (100° C.).
Embodiment 3
[0029] Get 95.8 parts of polytrimethylene terephthalate (PTT), 2 parts of magnesium oxide powder, 2 parts of zirconium dioxide powder, 0.2 part of N-beta-(aminoethyl)-gamma aminopropyltrimethoxysilane, After thorough mixing, extrude through twin-screw at 260°C and granulate. Manufacture the fiber cortex material; take 85 parts of low-melting point polyester (melting point: 150°C), 5 parts of polyethylene glycol, 5 parts of ethylene-vinyl acetate (EVA), 1 part of jasmonal, 2 parts of jasmone, and 3 parts of jasmonin Parts, after thorough mixing, twin-screw extrusion at 170°C, granulation. The fiber core layer material is produced; according to the sheath-to-core ratio of the fiber is 5:5, winding filaments are spun on the sheath-core composite spinning machine; then the fiber post-treatment is carried out according to Example 2 to obtain the functional fiber. It was determined that the far-infrared emissivity of the obtained fiber was 84% (100° C.).
PUM
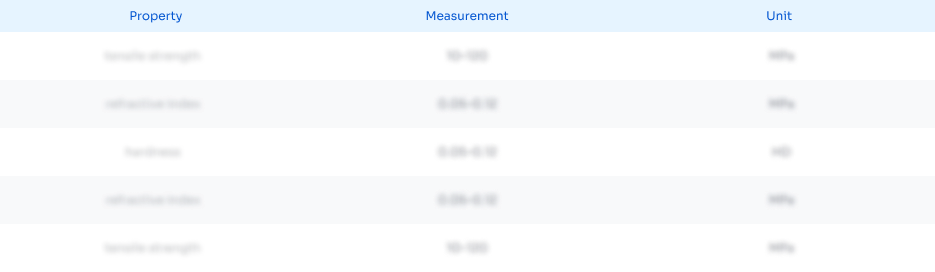
Abstract
Description
Claims
Application Information

- R&D
- Intellectual Property
- Life Sciences
- Materials
- Tech Scout
- Unparalleled Data Quality
- Higher Quality Content
- 60% Fewer Hallucinations
Browse by: Latest US Patents, China's latest patents, Technical Efficacy Thesaurus, Application Domain, Technology Topic, Popular Technical Reports.
© 2025 PatSnap. All rights reserved.Legal|Privacy policy|Modern Slavery Act Transparency Statement|Sitemap|About US| Contact US: help@patsnap.com