Injectiong coagulation shaping technology of high performance graphite product
A graphite product, injection molding technology, applied in clay products, applications, household appliances, etc., can solve the problems of high energy consumption in the molding process, inability to form at one time, complex shapes, etc., to achieve isotropy, improve reliability, reduce The effect of production costs
- Summary
- Abstract
- Description
- Claims
- Application Information
AI Technical Summary
Problems solved by technology
Method used
Image
Examples
Embodiment Construction
[0015] (1) Preparation of graphite carbon paste and related performance tests.
[0016] Weigh 150 grams of organic monomer acrylamide, 25 grams of crosslinking agent N,N'-methylenebisacrylamide, and 20 grams of dispersant sodium dodecylsulfonate, add it to distilled water, stir at room temperature, and make the above The reagents were fully dissolved and made into a 1000 ml solution, and the pH was adjusted to 11.0 with concentrated ammonia water; Ball milling at the speed of revolution per minute for a total of 24 hours to obtain graphite carbon slurry.
[0017] The carbon source in the present invention is natural graphite or synthetic graphite; the content of graphite in the carbon slurry is 20vol%-50vol%. The organic monomer is an organic compound containing vinyl, allyl, acrylate, acrylamide or acrylic functional groups, and the crosslinking agent is N, N'-methylenebisacrylamide; the sum of the content of the organic monomer and the crosslinking agent It is 5wt%-20wt% o...
PUM
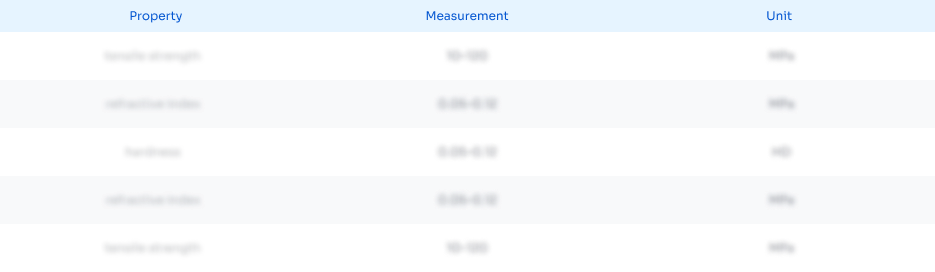
Abstract
Description
Claims
Application Information

- R&D
- Intellectual Property
- Life Sciences
- Materials
- Tech Scout
- Unparalleled Data Quality
- Higher Quality Content
- 60% Fewer Hallucinations
Browse by: Latest US Patents, China's latest patents, Technical Efficacy Thesaurus, Application Domain, Technology Topic, Popular Technical Reports.
© 2025 PatSnap. All rights reserved.Legal|Privacy policy|Modern Slavery Act Transparency Statement|Sitemap|About US| Contact US: help@patsnap.com