Method for recovering iron concentrate from blast furnace dust
A technology for blast furnace dust and iron recovery, applied in chemical instruments and methods, improvement of process efficiency, magnetic separation, etc., can solve the problems of small processing capacity, large water consumption, large floor area, etc., to improve the grade of iron metal, The effect of solving pollution and reducing the content of harmful element zinc
- Summary
- Abstract
- Description
- Claims
- Application Information
AI Technical Summary
Problems solved by technology
Method used
Image
Examples
Embodiment 1
[0013] Embodiment 1: referring to accompanying drawing, what the present invention is implemented is the dust of Meishan blast furnace, and its TFe is about 42%, Zn3.0%, Cl4%; Wherein strong magnetic mineral 25%, weak magnetic mineral about 50%, its The specific recycling process is as follows: (1) Pour the blast furnace dust with a moisture content of less than 10% into a mixing bucket, add water and stir for 15-20 minutes to make a 17% weight concentration slurry, and put it into a ¢300×200mm wet cylinder permanent magnet weak The magnetic separator 2 is selected, and the magnetic field strength is 80KA / m, and the strong magnetic minerals are first selected;
[0014] (2) The weak magnetic tailings enter the ¢300×200mm permanent magnetic drum type strong magnetic separator 3 for rough separation, and then use the ¢300×200mm permanent magnetic drum type strong magnetic separator 4 for rough separation of the tailings , to further reduce the grade of tailings; the magnetic fiel...
Embodiment 2
[0018] Embodiment 2: the magnetic separation intensity of the wet drum type permanent magnetic weak magnetic separator 2 is 90KA / m, the strong magnetic roughing magnetic field intensity is 610KA / m, and the sweeping magnetic field intensity is 770KA / m; all the other are identical with embodiment 1. After treatment by technological methods, the iron content of the iron concentrate increased from 42% to 54%, an increase of 12 percentage points; the zinc content of the iron concentrate dropped from 3.21% to 2.49%, a decrease of 0.9 percentage points, and the recovery rate of iron metal 76%.
PUM
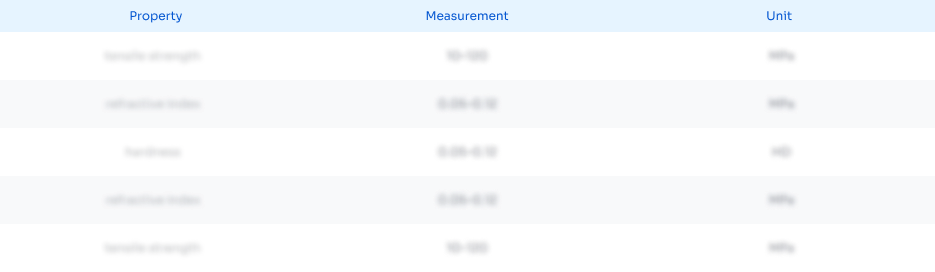
Abstract
Description
Claims
Application Information

- Generate Ideas
- Intellectual Property
- Life Sciences
- Materials
- Tech Scout
- Unparalleled Data Quality
- Higher Quality Content
- 60% Fewer Hallucinations
Browse by: Latest US Patents, China's latest patents, Technical Efficacy Thesaurus, Application Domain, Technology Topic, Popular Technical Reports.
© 2025 PatSnap. All rights reserved.Legal|Privacy policy|Modern Slavery Act Transparency Statement|Sitemap|About US| Contact US: help@patsnap.com