Method for preparing hydrogenation aromatization catalyst
A catalyst and aromatization technology, which is applied in the fields of refined hydrocarbon oil and petroleum industry, etc., can solve the problems that the hydrogenation activity of hydrogenation active metals is not fully exerted, the catalyst life cycle is short, and the aromatization activity is inhibited, etc. Effects of hydrodesulfurization activity, olefin content reduction, and strong aromatization ability
- Summary
- Abstract
- Description
- Claims
- Application Information
AI Technical Summary
Problems solved by technology
Method used
Examples
Embodiment 1
[0018] (1) Titanium dioxide and SB aluminum hydroxide modification
[0019] Add 60g of ammonium metatungstate and 18.3g of nickel nitrate into 100ml of deionized water to make a solution. Take 60ml of the solution, add 100g of industrial hydrated titanium oxide and 60g of SB aluminum hydroxide to the solution, stir evenly, let stand at room temperature for 8 hours, and then dry it at 110°C for 4 hours. Take it out, grind it, and pass through a 120-mesh sieve.
[0020] (2) ZSM-5 molecular sieve modification
[0021] 4g of zinc nitrate was dissolved in 20g of deionized water to make a solution. Add 80 g of ZSM-5 molecular sieves to the solution, stir evenly, let stand at room temperature for 8 hours, and then dry it at 110° C. for 6 hours. Take it out, grind it, and pass through a 120-mesh sieve.
[0022] (3) Catalyst preparation
[0023] After mixing 80g of ZSM-5 molecular sieve modified with zinc nitrate, titanium dioxide modified with ammonium metatungstate and nickel ni...
Embodiment 2
[0025] (1) Titanium dioxide and SB aluminum hydroxide modification
[0026] Add 60g of ammonium metatungstate, 14g of ammonium molybdate, and 18.3g of nickel nitrate into 100ml of deionized water to make a solution. Take 56ml of the solution, add 100g of industrial hydrated titanium dioxide and 60g of SB aluminum hydroxide to the solution, stir evenly, let stand at room temperature for 6 hours, and then dry it at 120°C for 6 hours. Take it out, grind it, and pass through a 120-mesh sieve.
[0027] (2) ZSM-5 molecular sieve modification
[0028] 4g of zinc nitrate was dissolved in 20g of deionized water to make a solution. Add 80 g of ZSM-5 molecular sieves to the solution, stir evenly, let stand at room temperature for 10 hours, and then dry it at 120° C. for 4 hours. Take it out, grind it, and pass through a 100-mesh sieve.
[0029] (3) Catalyst preparation
[0030] After mixing 80g of ZSM-5 molecular sieve modified with zinc nitrate, titanium dioxide modified with ammon...
Embodiment 3
[0032] (1) Titanium dioxide and SB aluminum hydroxide modification
[0033] Add 50 g of ammonium molybdate and 36.6 g of nickel nitrate into 100 ml of deionized water to prepare a solution. Take 70ml of the solution, add 100g of industrial hydrated titanium dioxide and 60g of SB aluminum hydroxide to the solution, stir evenly, let stand at room temperature for 8 hours, and then dry it at 120°C for 6 hours. Take it out, grind it, and pass through a 120-mesh sieve.
[0034] (2) ZSM-5 molecular sieve modification
[0035] 2.8g of ammonium dihydrogen phosphate was dissolved in 20g of deionized water to make a solution. Add 80 g of ZSM-5 molecular sieves to the solution, stir evenly, let stand at room temperature for 6 hours, and then dry it at 120° C. for 5 hours. Take it out, grind it, and pass through a 110-mesh sieve.
[0036] (3) Catalyst preparation
[0037] After mixing 80g of ZSM-5 molecular sieve modified by ammonium dihydrogen phosphate, titanium dioxide modified by ...
PUM
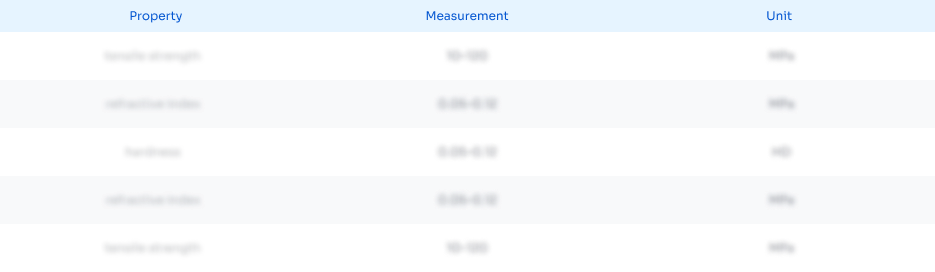
Abstract
Description
Claims
Application Information

- R&D
- Intellectual Property
- Life Sciences
- Materials
- Tech Scout
- Unparalleled Data Quality
- Higher Quality Content
- 60% Fewer Hallucinations
Browse by: Latest US Patents, China's latest patents, Technical Efficacy Thesaurus, Application Domain, Technology Topic, Popular Technical Reports.
© 2025 PatSnap. All rights reserved.Legal|Privacy policy|Modern Slavery Act Transparency Statement|Sitemap|About US| Contact US: help@patsnap.com